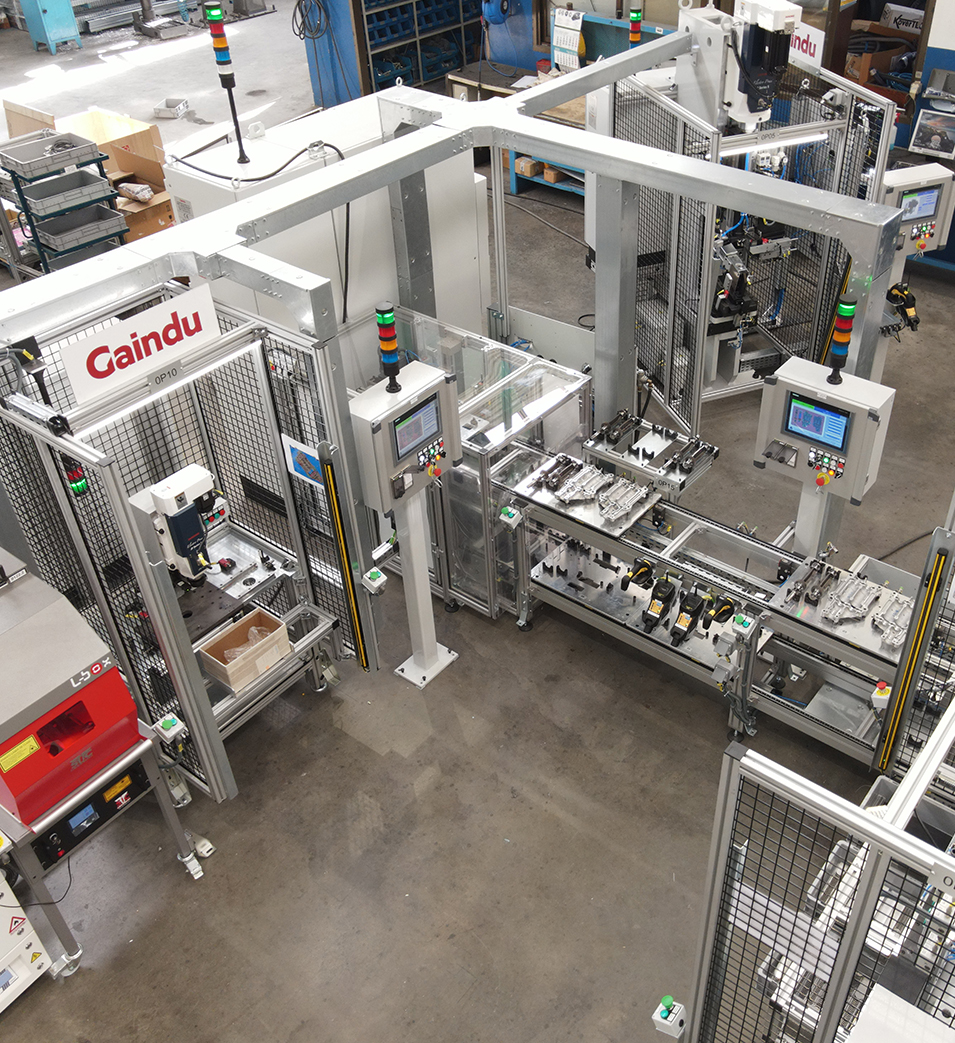
Herausforderung
Die Herausforderung bei diesem Projekt bestand in der Optimierung der Effizienz, Präzision und Rückverfolgbarkeit des Produktionsprozesses für die Ausgleichswellenmodule unseres Kunden, einer wichtigen Komponente im Automobilbau.
Aufgrund der spezifischen Produktionsanforderungen für dieses Projekt wurde ein ausgeklügeltes und effizientes System benötigt, das mehrere Stationen sowohl online als auch offline integriert, um einen nahtlosen Arbeitsablauf und hohe Präzision zu gewährleisten.
Bei Gaindu waren wir für die Konzeption einer voll integrierten und automatisierten Montagelinie für die Ausgleichswellenmodule verantwortlich. Die Montagelinie besteht aus mehreren manuellen, halbautomatischen und automatischen Stationen sowie vier zusätzlichen Offline-Stationen zur Unterstützung wichtiger Hilfsvorgänge.
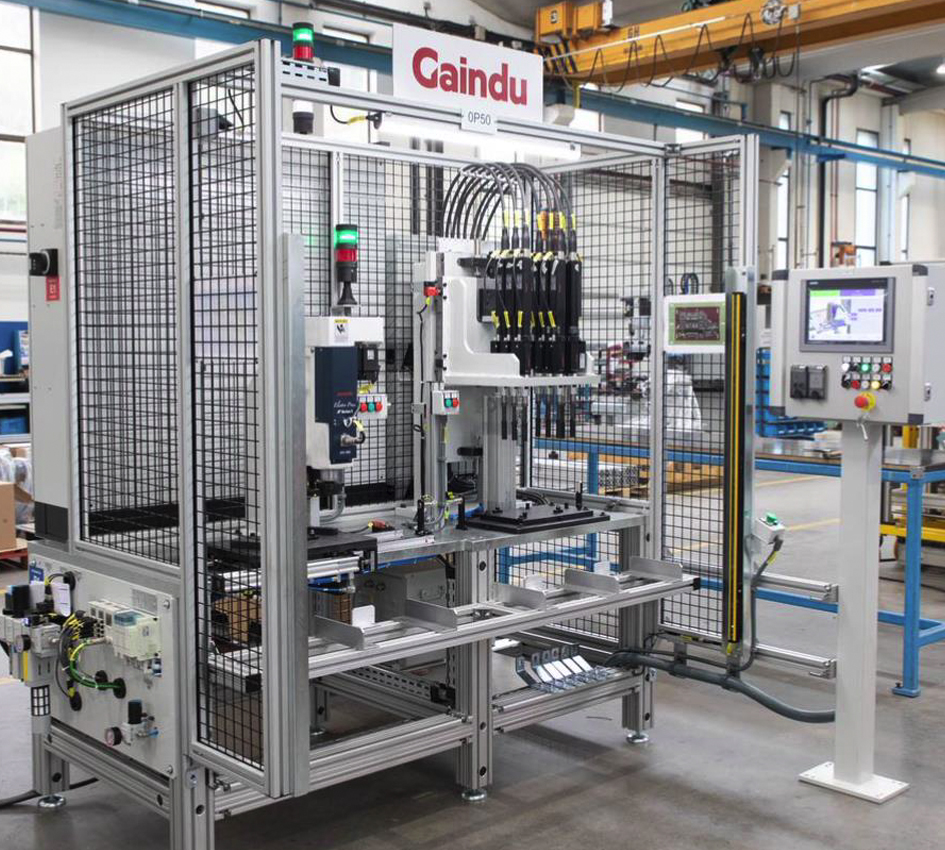
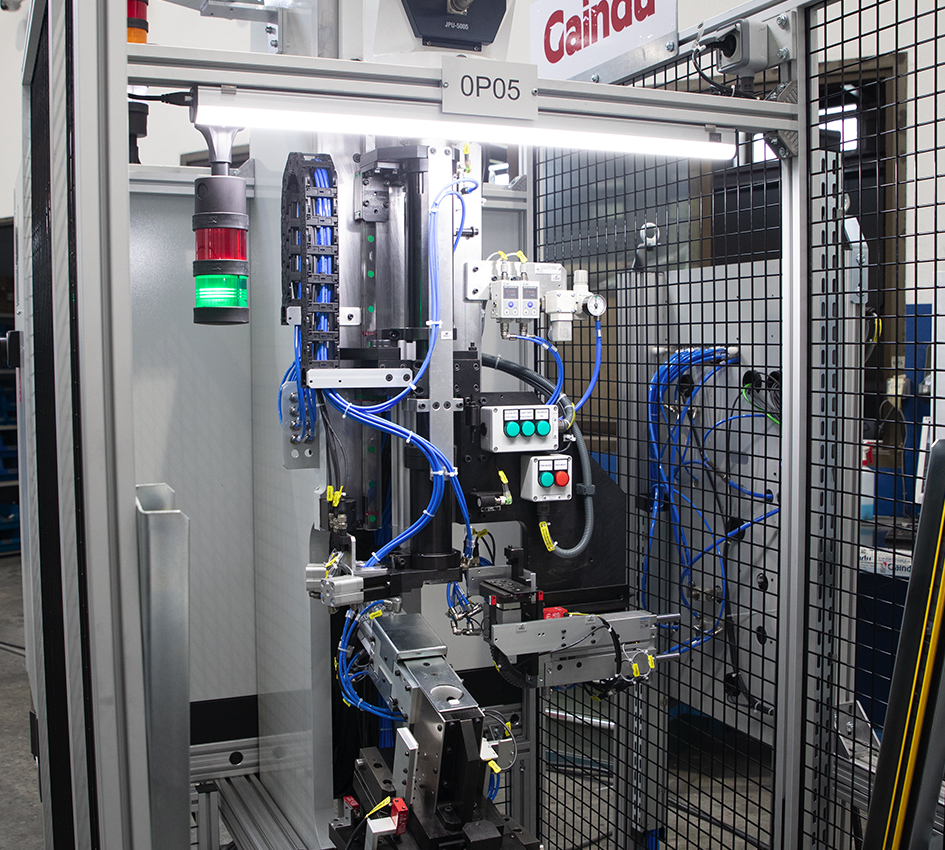
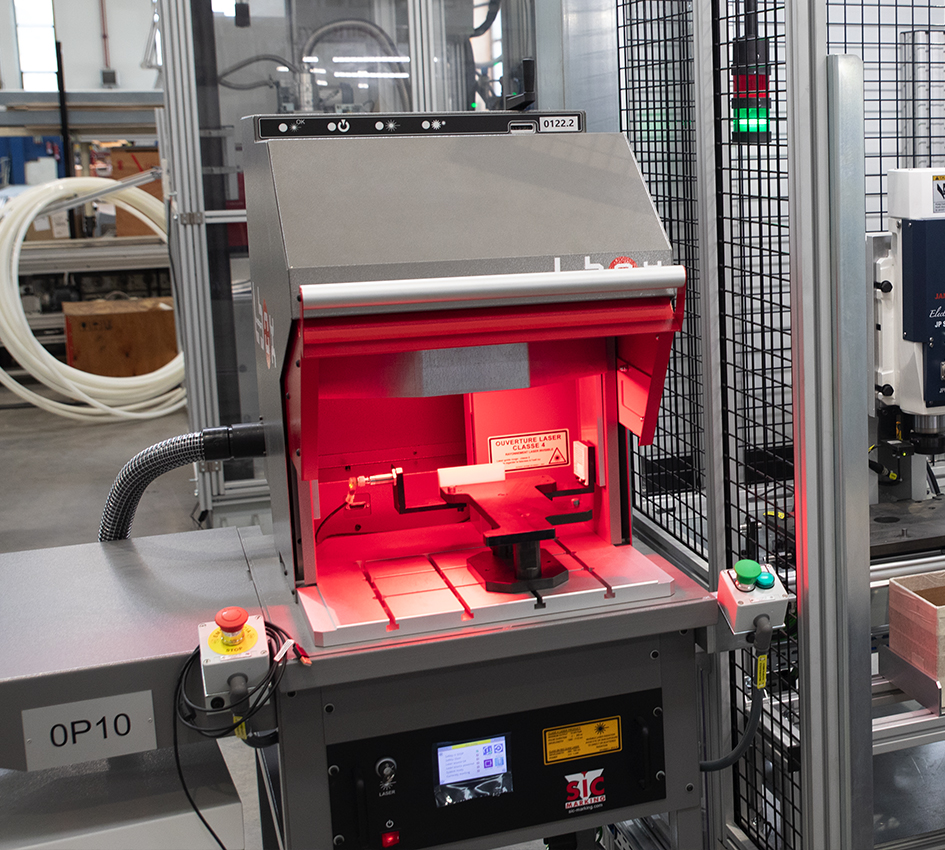
ARBEITSFOLGEN
Hilfsstationen | Lasermarkierung
Am Anfang der Linie wird in einer separaten Markierungsstation ein 2D-Code auf die Oberseite gelasert. Diese Station ist mit einer Laserschutzkabine der Klasse 4 ausgestattet, um die Sicherheit des Bedieners zu gewährleisten.
Die Anlage umfasst ein Rauch- und Partikelabsaugsystem für die während des Prozesses entstehenden Emissionen sowie eine Sichtkamera zur Überprüfung der korrekten Ausrichtung.
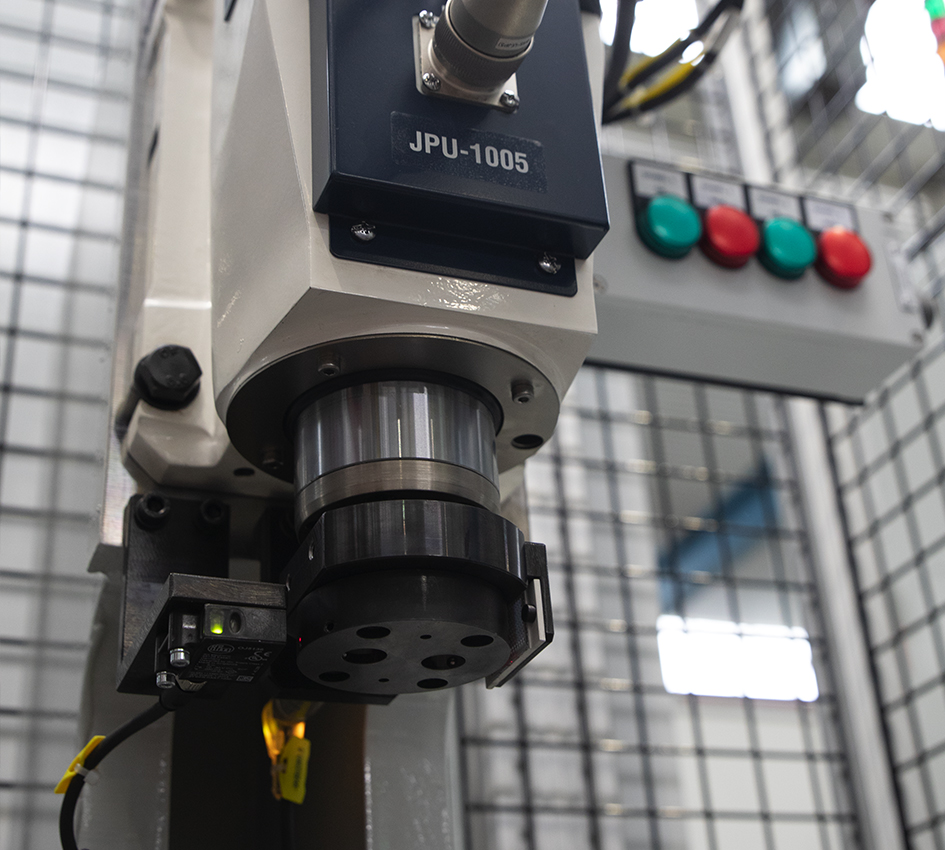
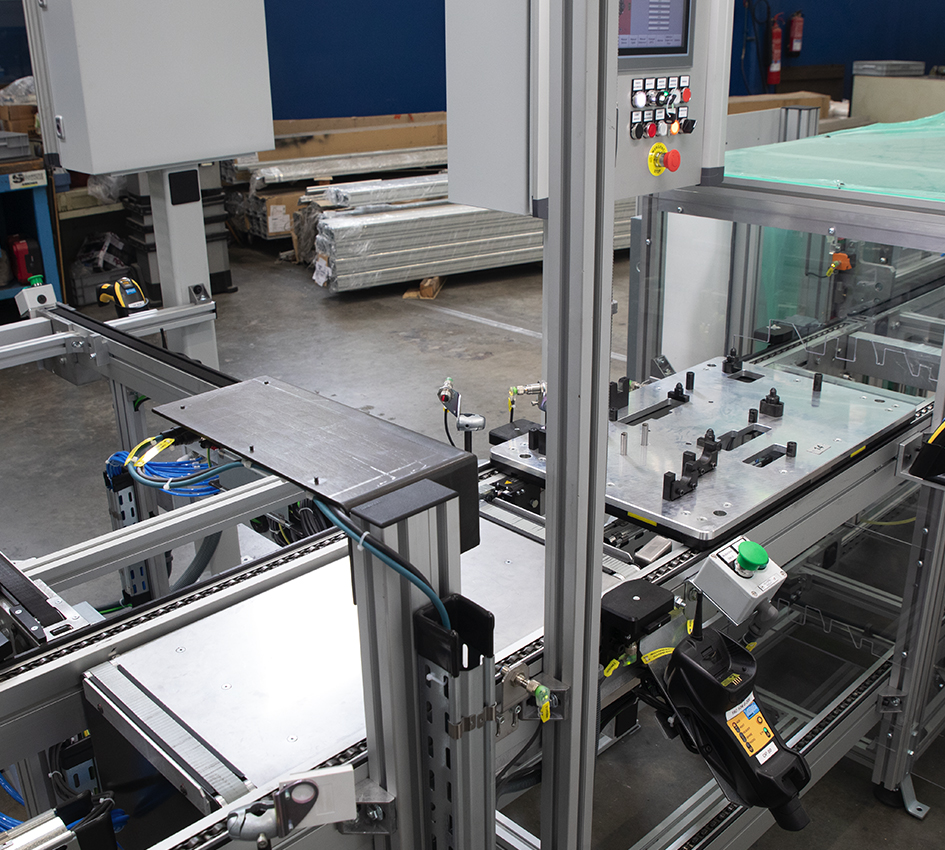
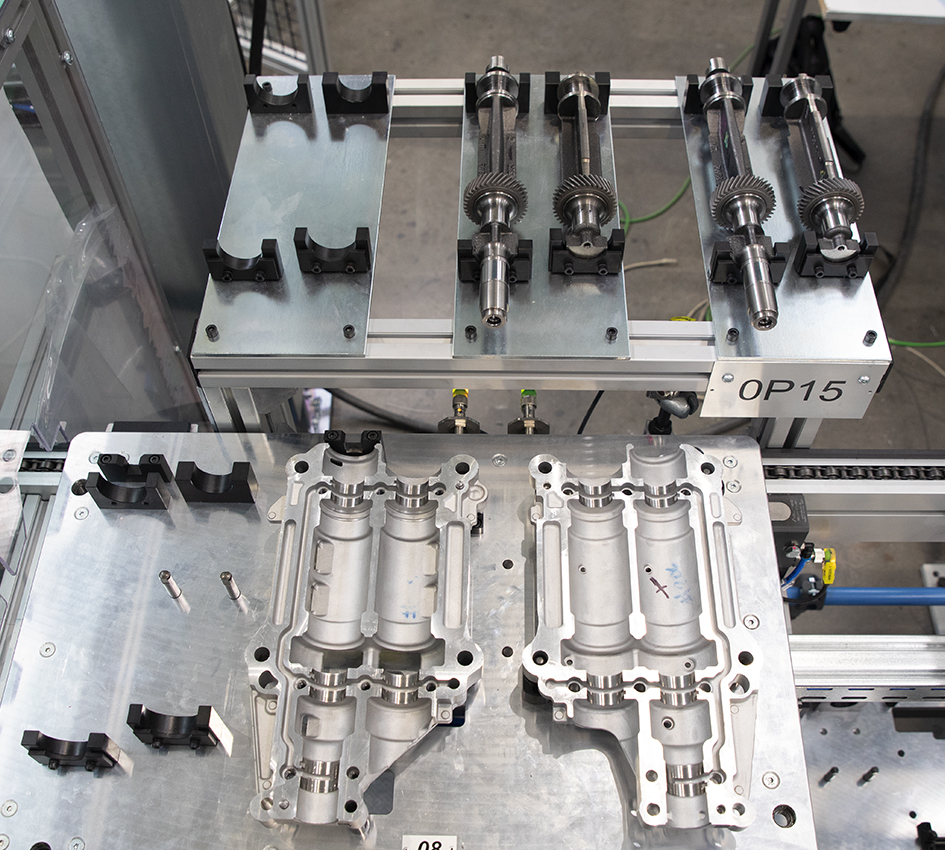
ARBEITSFOLGEN
In-Line-Stationen | Beladung des Montagesatzes auf die Palette
An der ersten Station des Palettenförderers werden die zu montierenden Komponenten (Gehäuse und Wellen) auf eine Palette geladen, die die Teile durch die Montagelinie befördert.
An dieser Station wird der 2D-Code auf den Gehäusen und Wellen vom Bediener mit Handscannern gelesen. Auf diese Weise werden alle Komponenten mit dem im vorherigen Arbeitsgang markierten 2D-Code verknüpft, was eine vollständige Rückverfolgbarkeit der montierten Baugruppe ermöglicht.
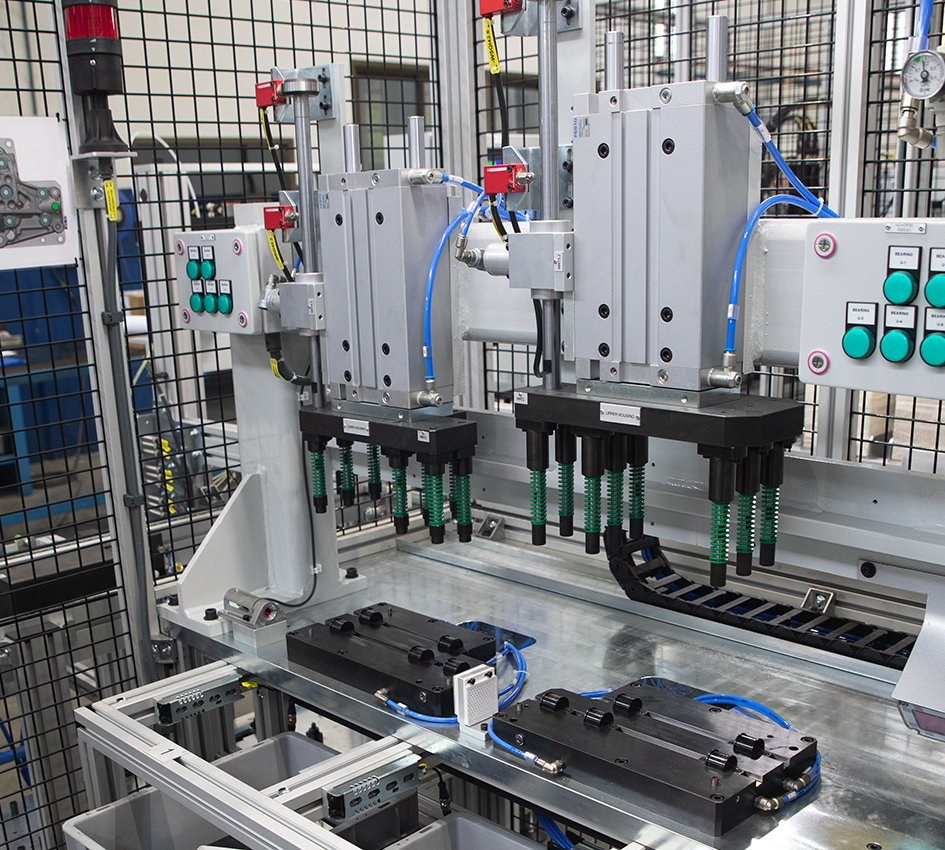
ARBEITSFOLGEN
In-Line-Stationen | Lagermontage
Es werden 3 verschiedene Lagermodelle montiert. Die Wahl des Lagermodells basiert auf den Abmessungen der Wellen und Gehäuse, die in den 2D-Codes der einzelnen Komponenten angegeben sind. Um sicherzustellen, dass das richtige Lager ausgewählt wird, verfügt jede Sammelbox über ein lichtbasiertes Auswahlsystem und eine manuelle Durchgangserkennung.
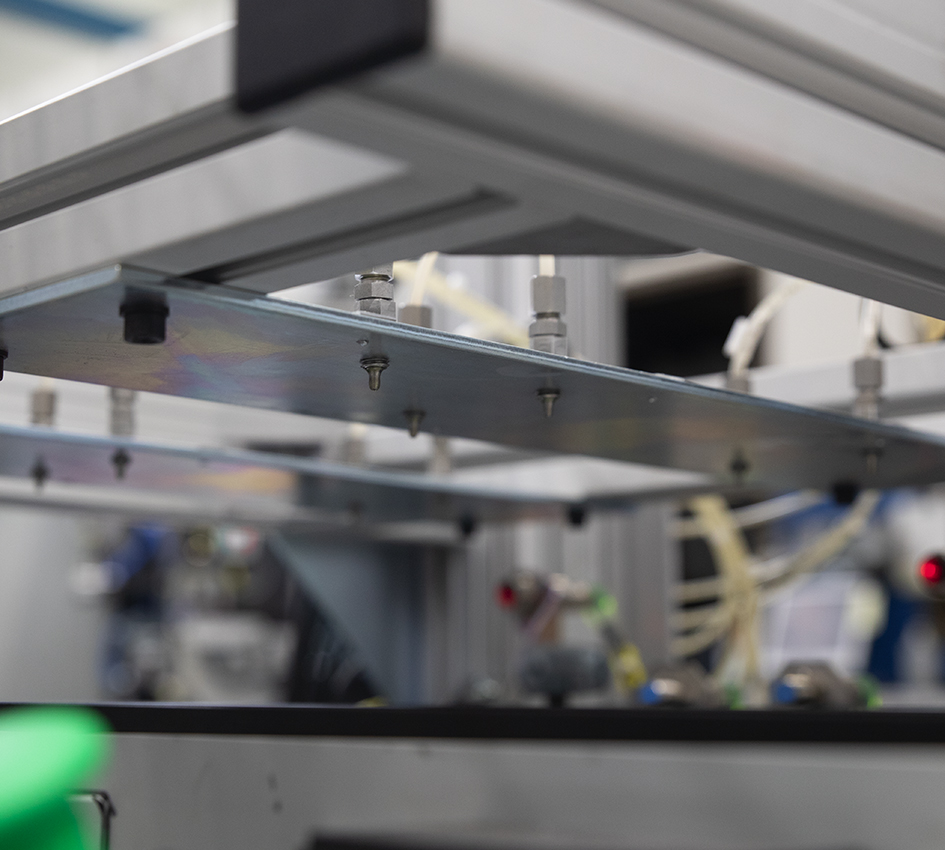
ARBEITSFOLGEN
In-Line-Stationen | Ölen & Schächte Maschenbildung und Belastung
An der ersten Haltestelle werden die Lager über automatische Schmierdüsen geschmiert. Beim nächsten Halt kuppelt der Bediener die Wellen ein und lädt sie in das Gehäuse.
Ein mechanisches Poka-Yoke prüft die korrekte Winkellage der eingerasteten Wellen. Dann setzt der Bediener das obere Gehäuse auf das untere und schiebt die Bolzen manuell ein.
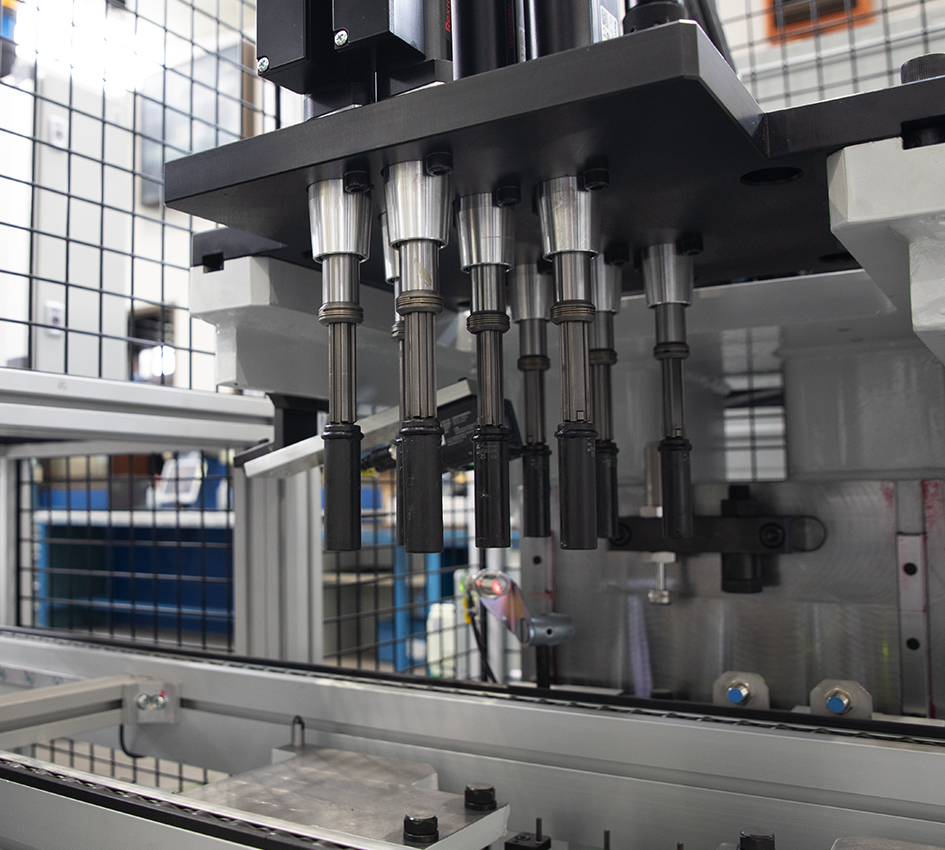
ARBEITSFOLGEN
In-Line-Stationen | Automatisches Anziehen von Bolzen
Die Palette kommt an der Schraubstation an, und alle Schrauben werden gleichzeitig mit mehreren drehmomentgesteuerten Spindeln angezogen. Eine Schraube ist anders (kürzer) als die anderen, daher wird die korrekte Position aller Schrauben durch Sensoren überwacht.
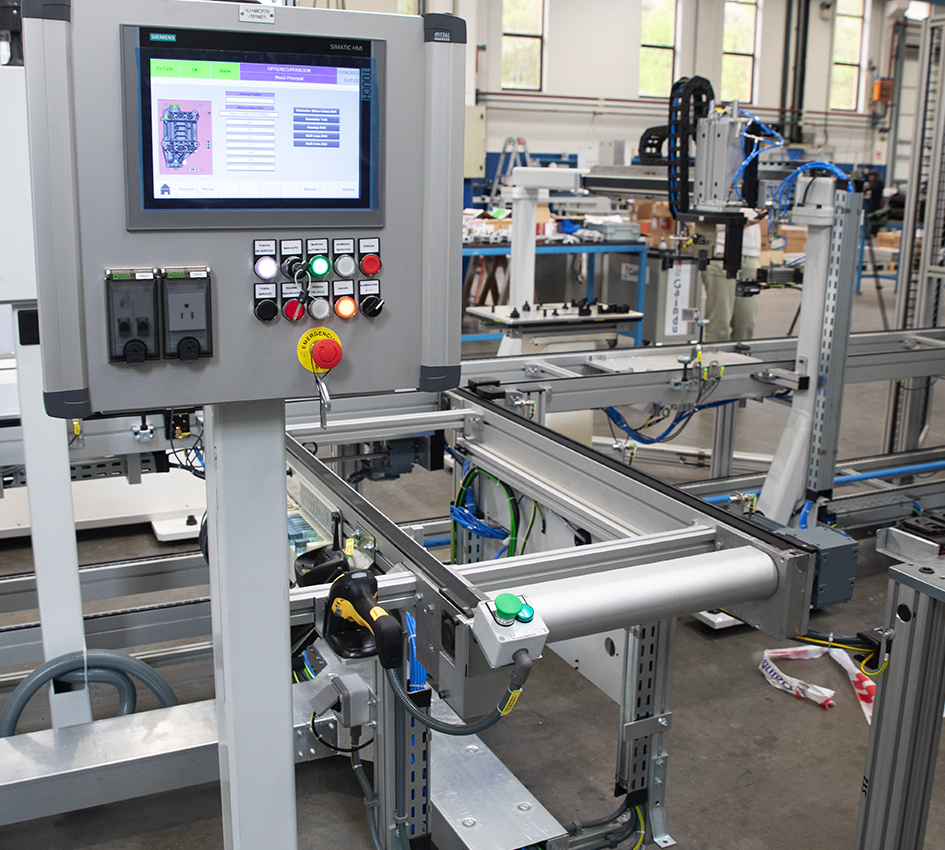
ARBEITSFOLGEN
In-Line-Stationen | Rework-Station
Vor der Endkontrolle liest eine Kamera den 2D-Code auf dem Gehäuse. Wenn einer der vorangegangenen Vorgänge fehlerhaft war, wird die Palette automatisch auf ein Ausschussband befördert. Am Ende dieses Rückweisungsbandes zeigt ein HMI den Grund an, warum ein Teil NOK (nicht in Ordnung) ist, und es gibt einen Arbeitsplatz, an dem das gesamte Gehäuse demontiert wird.
Integrierte Technologien
FALLSTUDIE HERUNTERLADENMöchten Sie mehr darüber erfahren, wie wir Sie unterstützen können?
KONTAKTIEREN SIE UNS