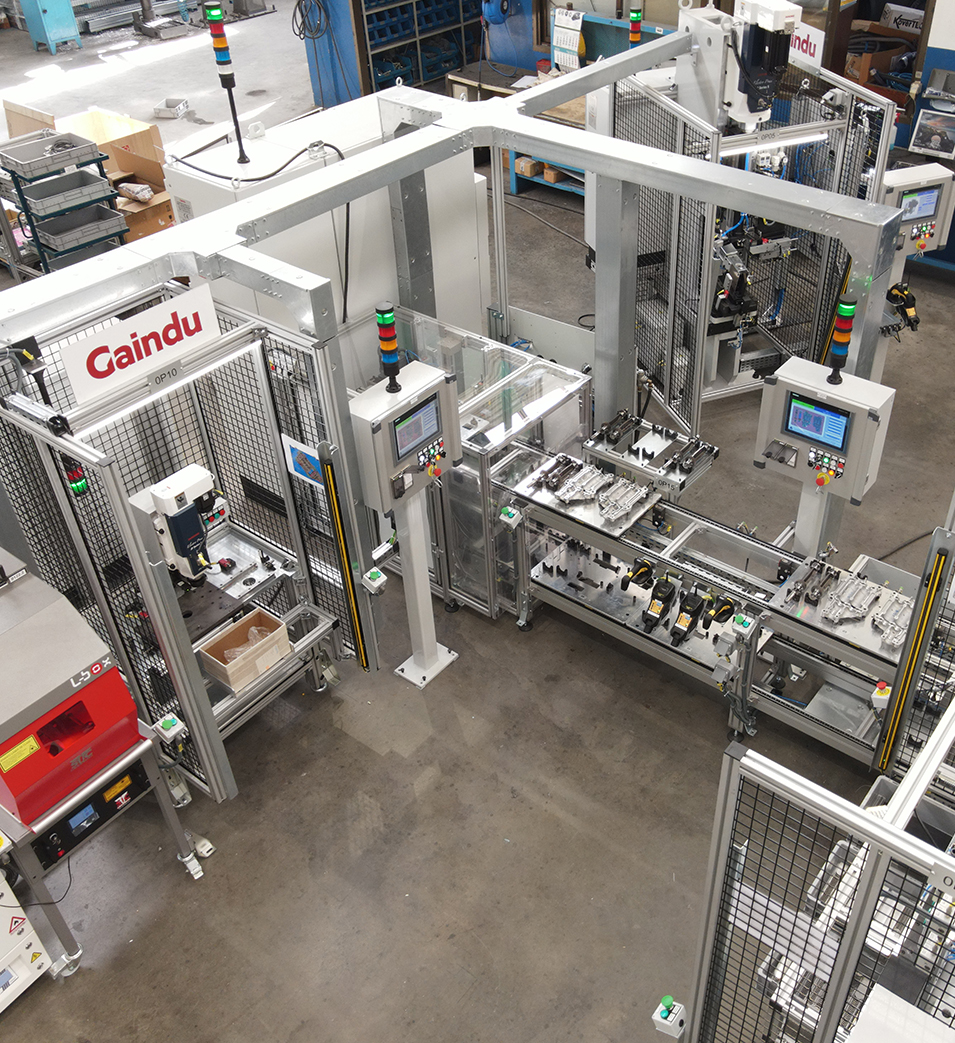
Défi
Le défi de ce projet consistait à optimiser l'efficacité, la précision et la traçabilité du processus de production des modules d'arbres de compensation de notre client, un composant important dans l'ingénierie automobile.
En raison des exigences de production spécifiques à ce projet, un système plus sophistiqué et plus efficace était nécessaire, intégrant de multiples stations à la fois en ligne et hors ligne pour assurer un flux de travail continu et une grande précision.
Chez Gaindu, nous avons été chargés de concevoir une ligne d'assemblage entièrement intégrée et automatisée pour les modules de l'arbre de compensation. La ligne d'assemblage se compose de plusieurs stations manuelles, semi-automatiques et automatiques, ainsi que de quatre stations hors ligne supplémentaires pour prendre en charge les opérations auxiliaires critiques.
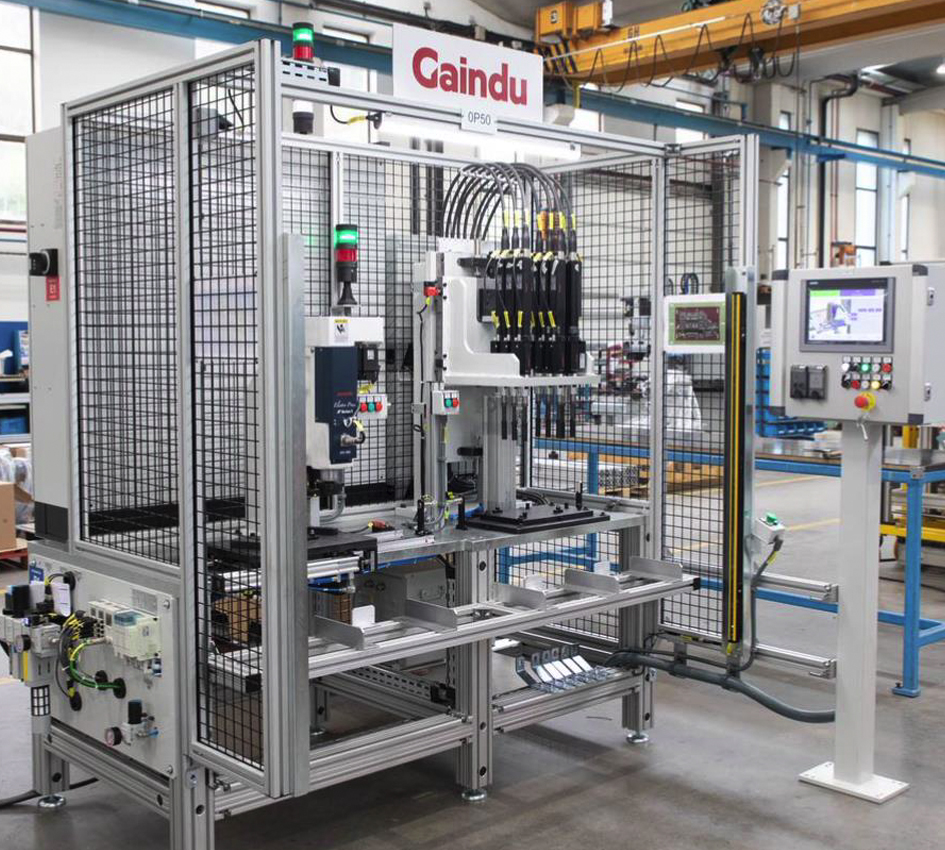
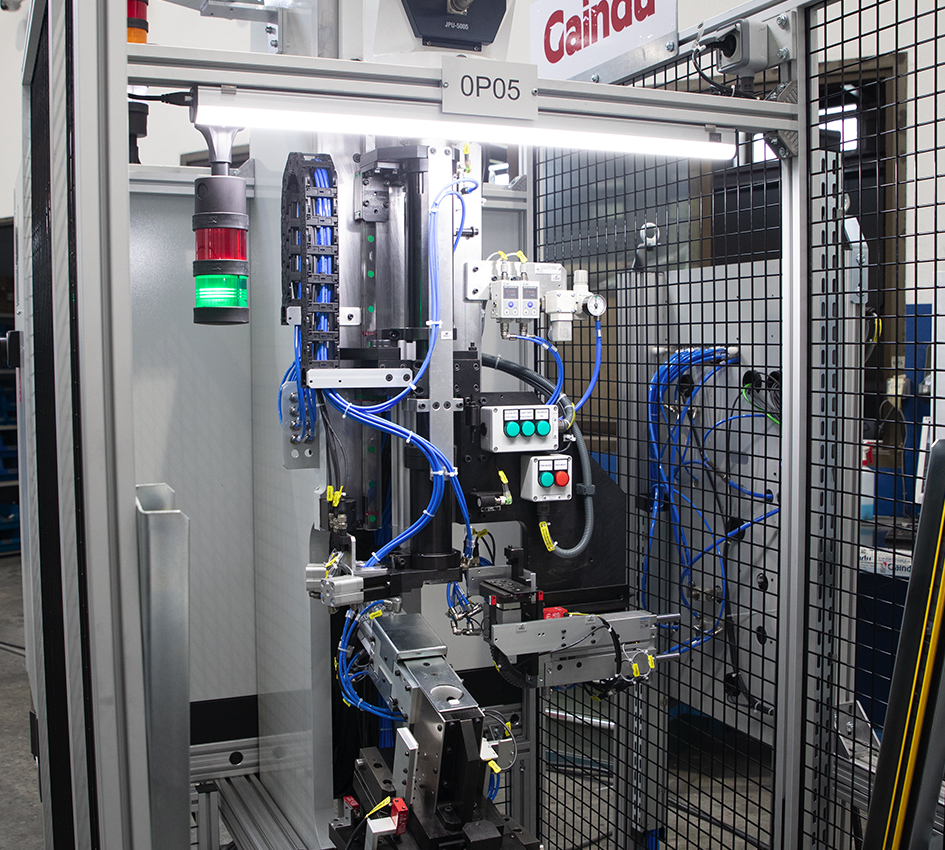
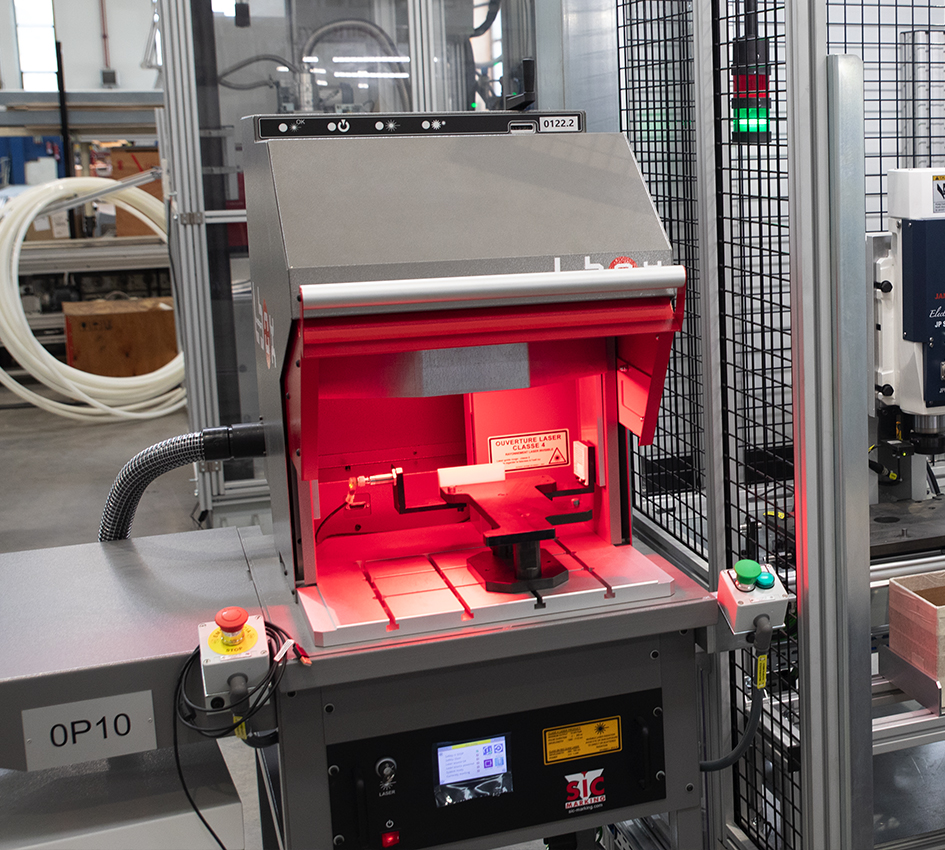
OPERATIONS
Stations auxiliaires | Marquage laser
Au début de la ligne, un code 2D est marqué au laser sur la partie supérieure dans une station de marquage séparée. Cette station est équipée d'une enceinte de protection laser de classe 4 pour garantir la sécurité de l'opérateur.
L'équipement comprend un système d'extraction des fumées et des particules pour les émissions générées au cours du processus, ainsi qu'une inspection par caméra de vision pour vérifier l'alignement correct.
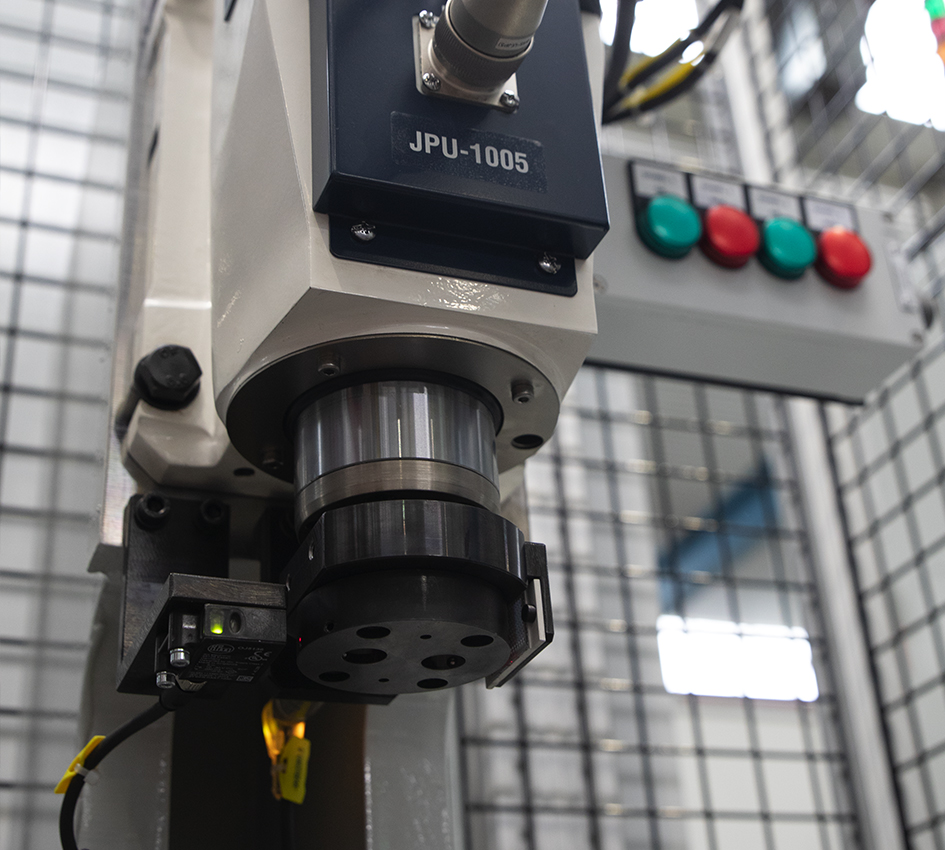
OPERATIONS
Stations auxiliaires | Assemblage de goupilles
2 goupilles sont pressées dans le boîtier inférieur à l'aide d'une presse électrique dont la force et la position sont contrôlées. Le marquage du boîtier supérieur et l'assemblage des goupilles sur le boîtier inférieur sont effectués en parallèle.
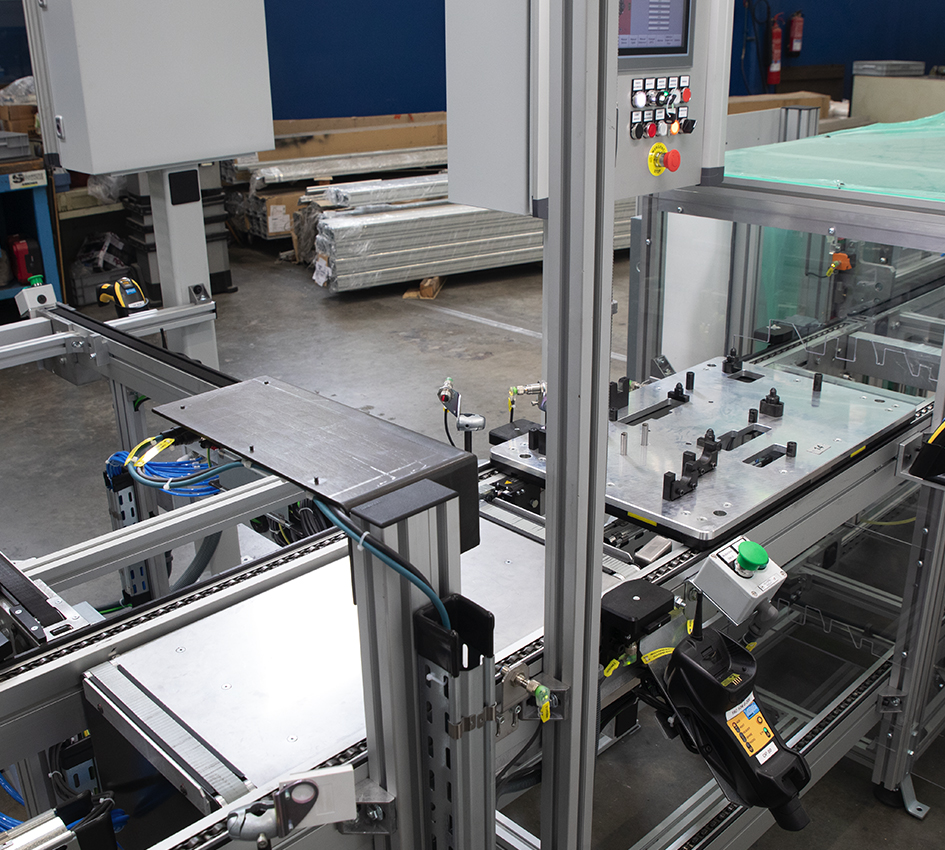
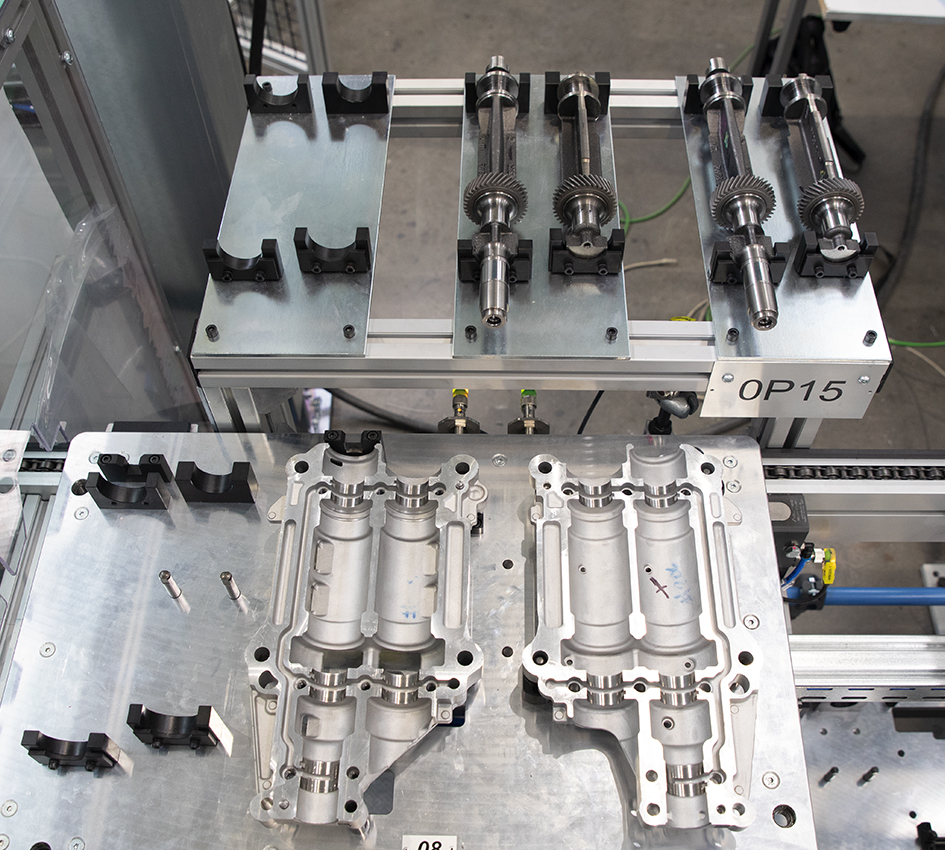
OPERATIONS
Stations en ligne | Chargement des ensembles sur la palette
Au premier poste du convoyeur palettisé, les composants à assembler (boîtiers et arbres) sont chargés sur une palette qui déplacera les pièces tout au long de la chaîne d'assemblage.
À cette station, le code 2D des boîtiers et des arbres est lu par l'opérateur à l'aide de scanners portatifs. De cette manière, tous les composants sont liés au code 2D marqué lors de l'opération précédente, ce qui permet une traçabilité complète de l'ensemble assemblé.
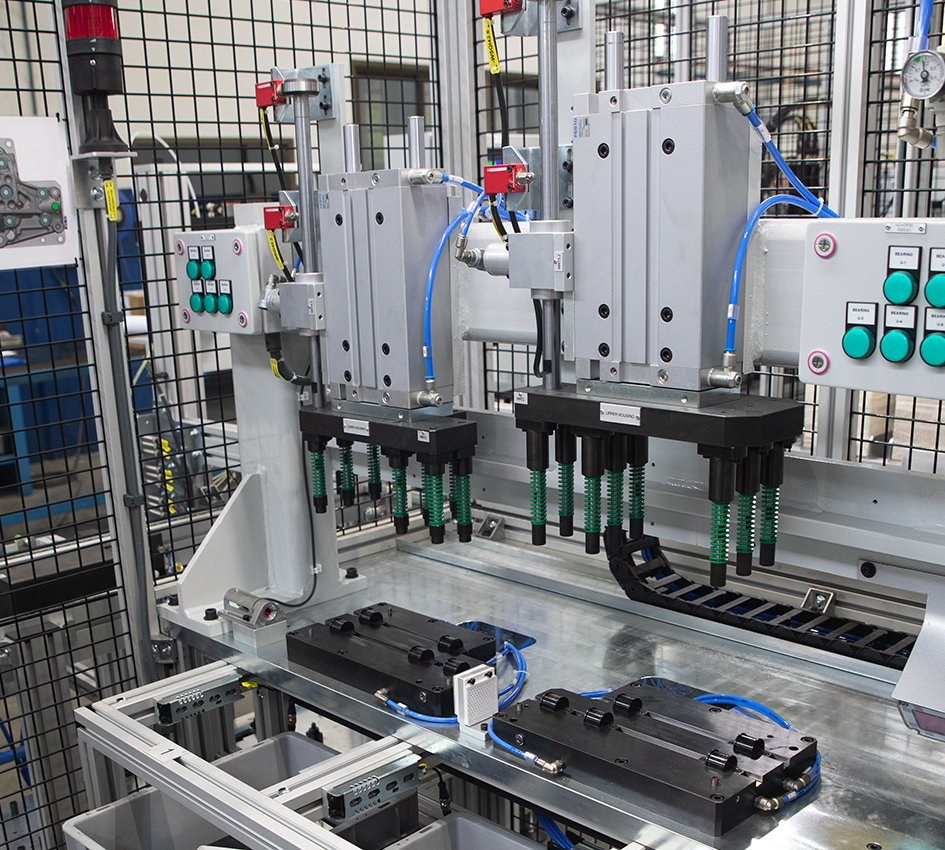
OPERATIONS
Stations en ligne | Assemblage de paliers
3 modèles de roulements différents sont assemblés. Le choix du modèle de roulement est basé sur les dimensions des arbres et des boîtiers indiquées dans les codes 2D de chaque composant. Pour s'assurer que le bon roulement est sélectionné, chaque boîte de collecte sera équipée d'un système de sélection lumineux et d'une détection manuelle du passage.
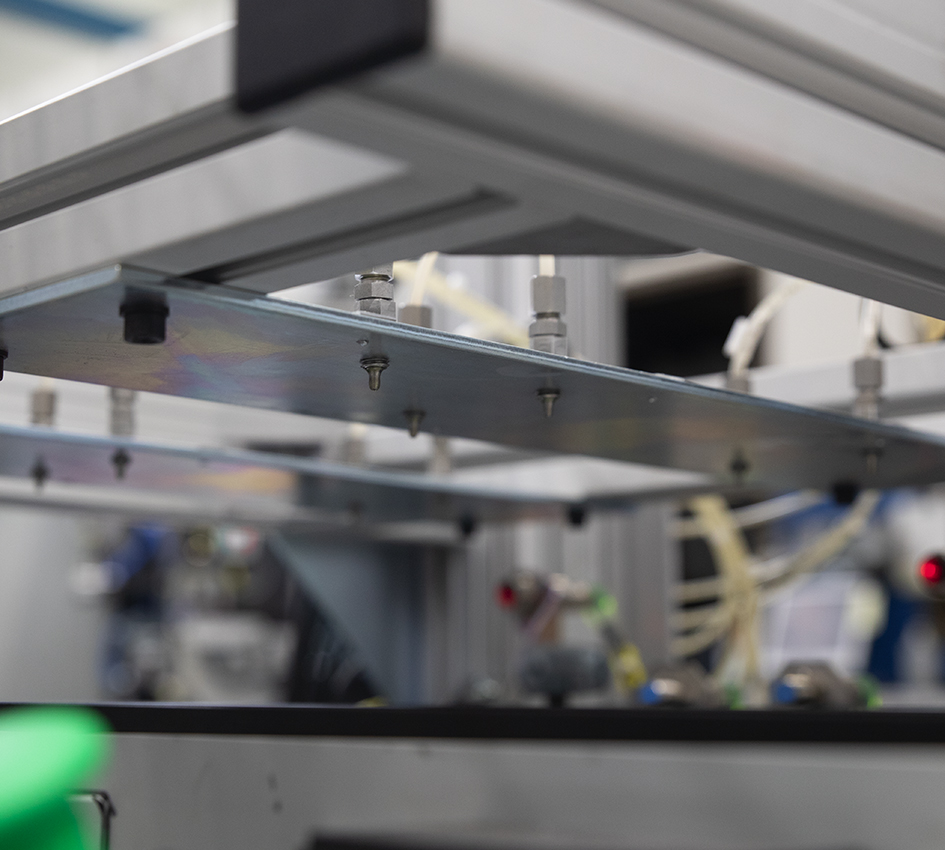
OPERATIONS
Stations en ligne | Engrènement et chargement d'arbres et de lubrifiants
Au premier arrêt, les roulements sont graissés à l'aide de buses de graissage automatiques. À l'arrêt suivant, l'opérateur engage les arbres et les charge dans le boîtier.
Un poka-yoke mécanique vérifie la position angulaire correcte des arbres engagés. Ensuite, l'opérateur place le carter supérieur sur le carter inférieur et introduit manuellement les boulons.
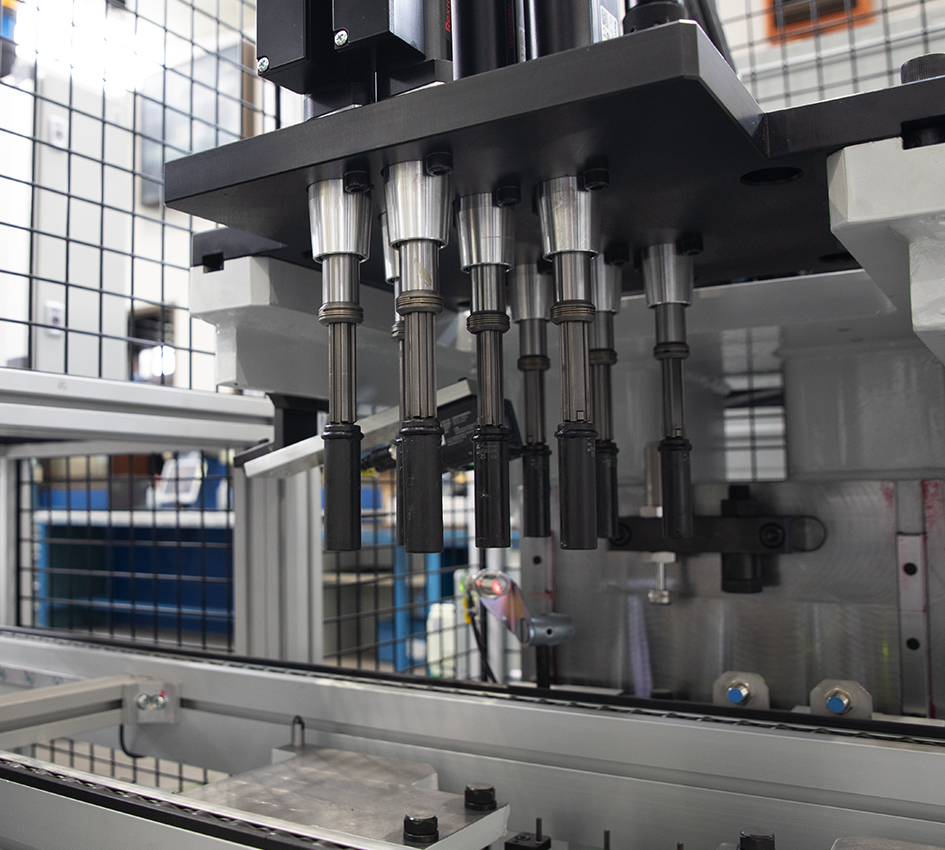
OPERATIONS
Stations en ligne | Serrage automatique des boulons
La palette arrive à la station de serrage et tous les boulons sont serrés simultanément à l'aide de plusieurs broches à contrôle de couple. Un boulon étant différent (plus court) des autres, la position correcte de tous les boulons est contrôlée par des capteurs.
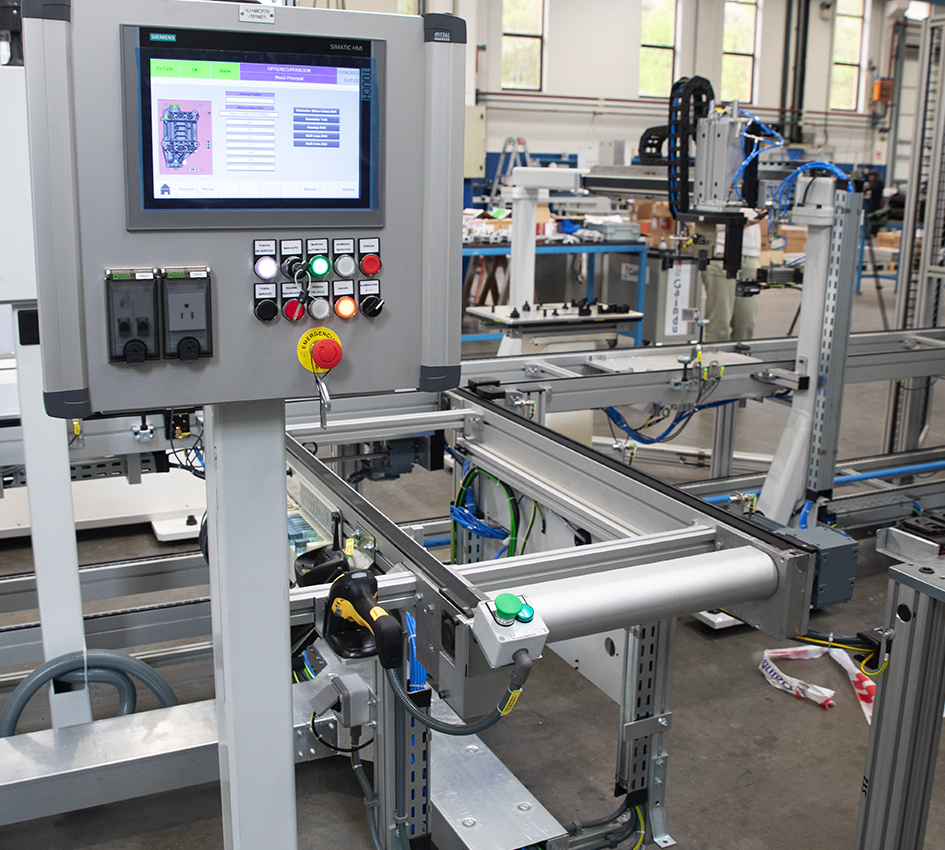
OPERATIONS
Stations en ligne | Station de reprise
Avant l'inspection finale, une caméra lit le code 2D sur le boîtier. Si l'une des opérations précédentes était incorrecte, la palette est automatiquement déplacée vers un convoyeur de rejet. Au bout de ce convoyeur de rejet, une IHM affiche la raison pour laquelle une pièce est NOK (not okay), et un poste de travail permet de désassembler l'ensemble du boîtier.
Technologies intégrées
TÉLÉCHARGER L'ÉTUDE DE CASVous souhaitez en savoir plus?
CONTACTEZ-NOUS