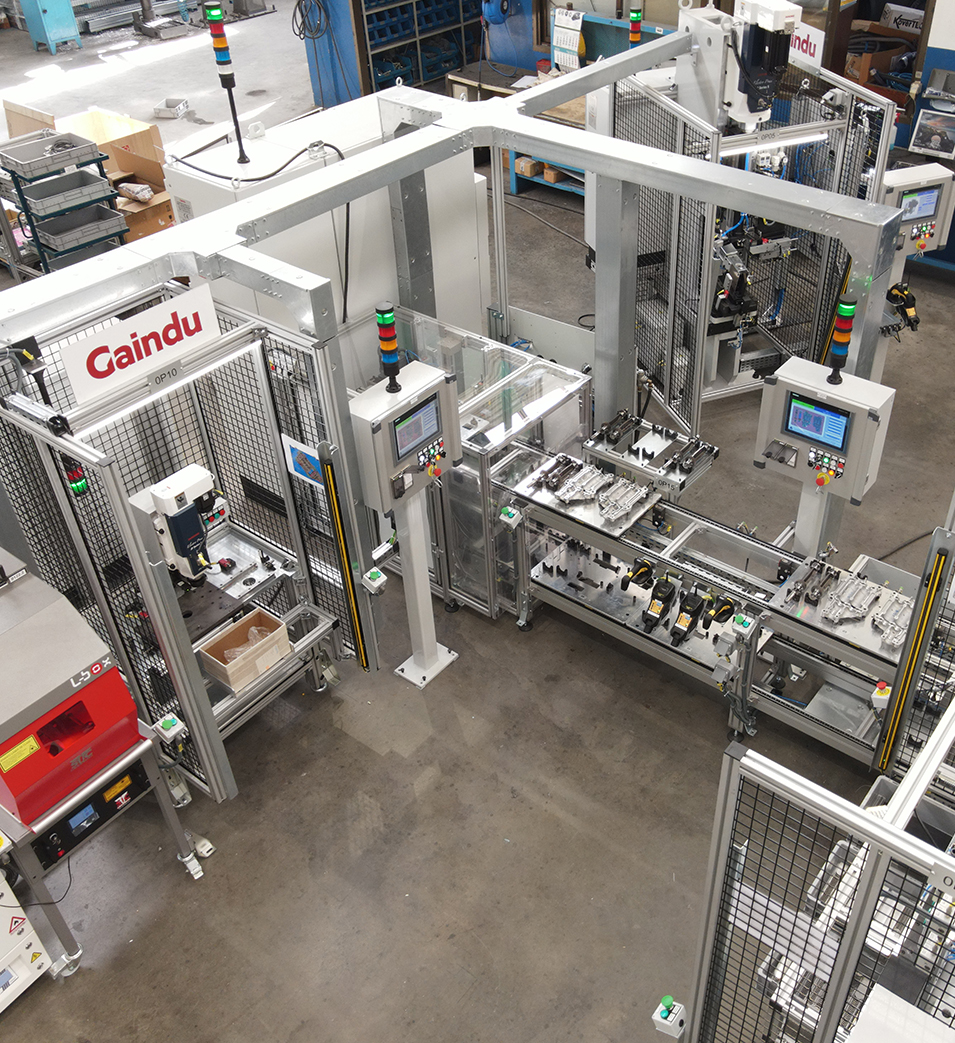
Challenger
The challenge of this project involved optimizing the efficiency, precision, and traceability of the production process for our client's balance shaft modules, a important component in automotive engineering.
Due to the specific production requirements for this project, a more sophisticated and efficient system was needed, integrating multiple stations both online and offline to ensure a seamless workflow and high precision.
At Gaindu, we were responsible for designing a fully integrated and automated assembly line for the balance shaft modules. The assembly line consists of several manual, semi-automatic, and automatic stations, with an additional four offline stations to support critical auxiliary operations.
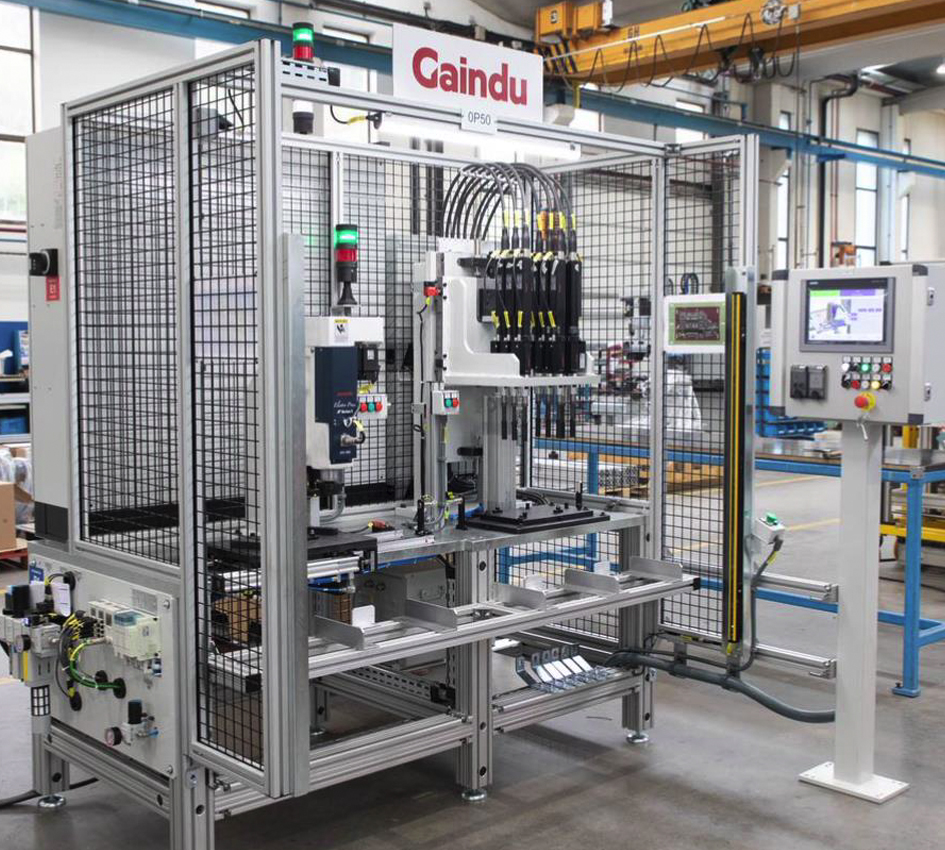
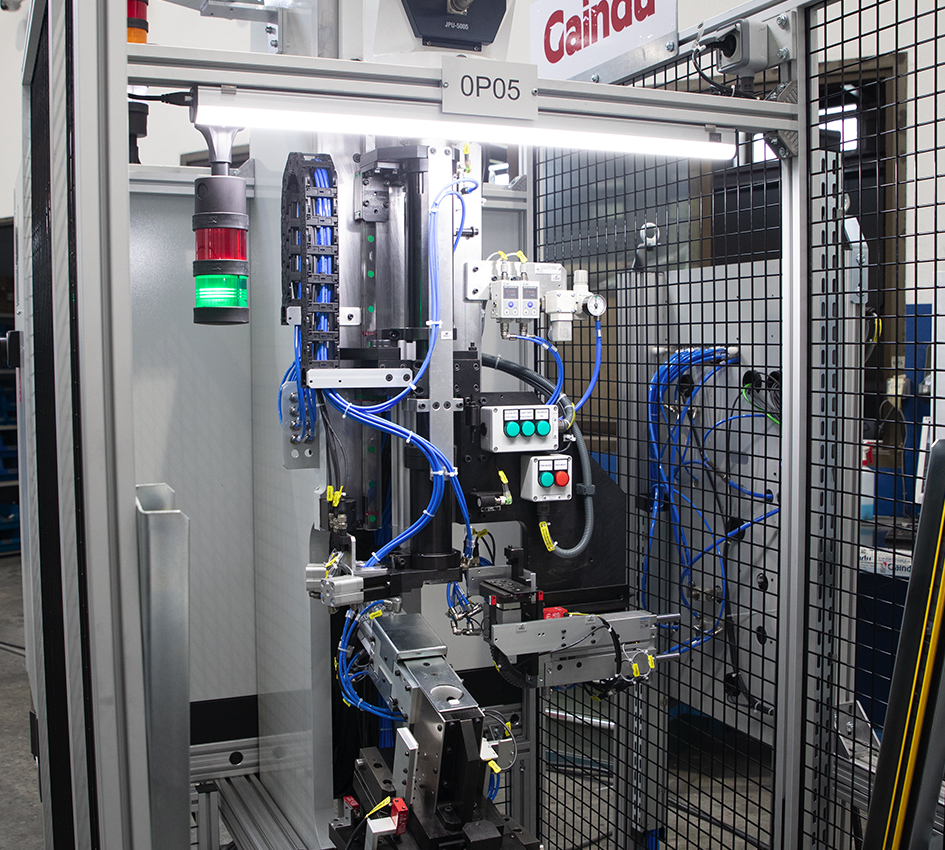
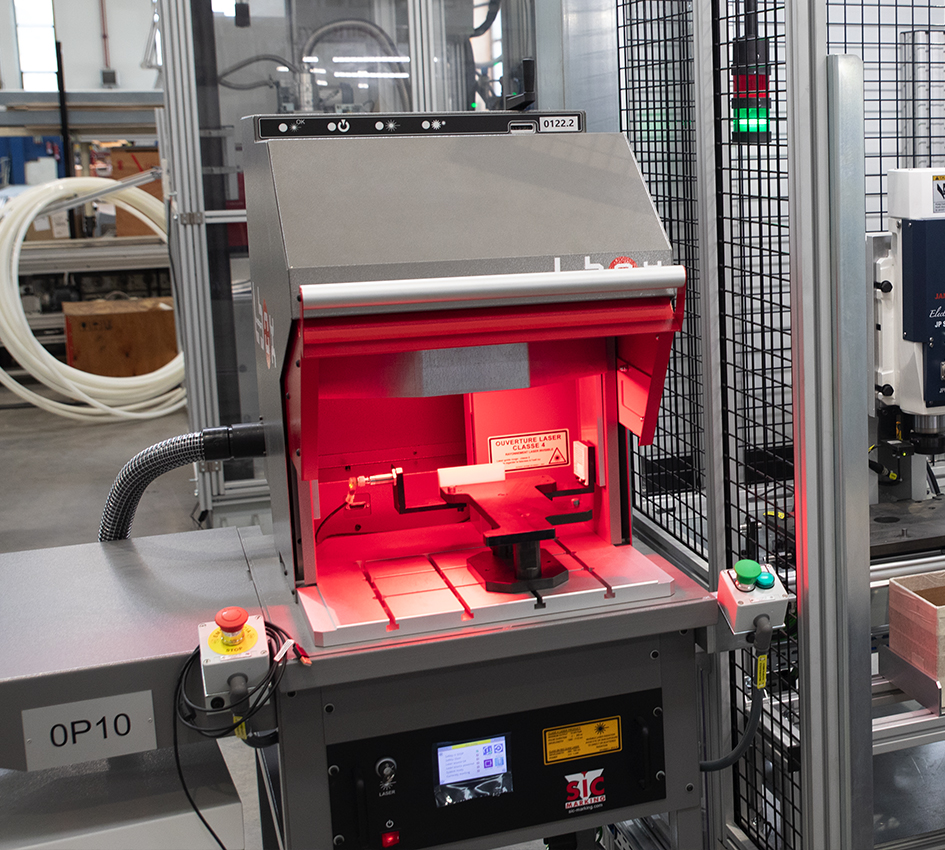
OPERATIONS
Auxiliary Stations | Laser Marking
At the beginning of the line, a 2D code is laser-marked on the top at a separate marking station. This station has a Class 4 laser protection enclosure to ensure operator safety.
The equipment includes a smoke and particle extraction system for emissions generated during the process, as well as vision camera inspection to verify proper alignment.
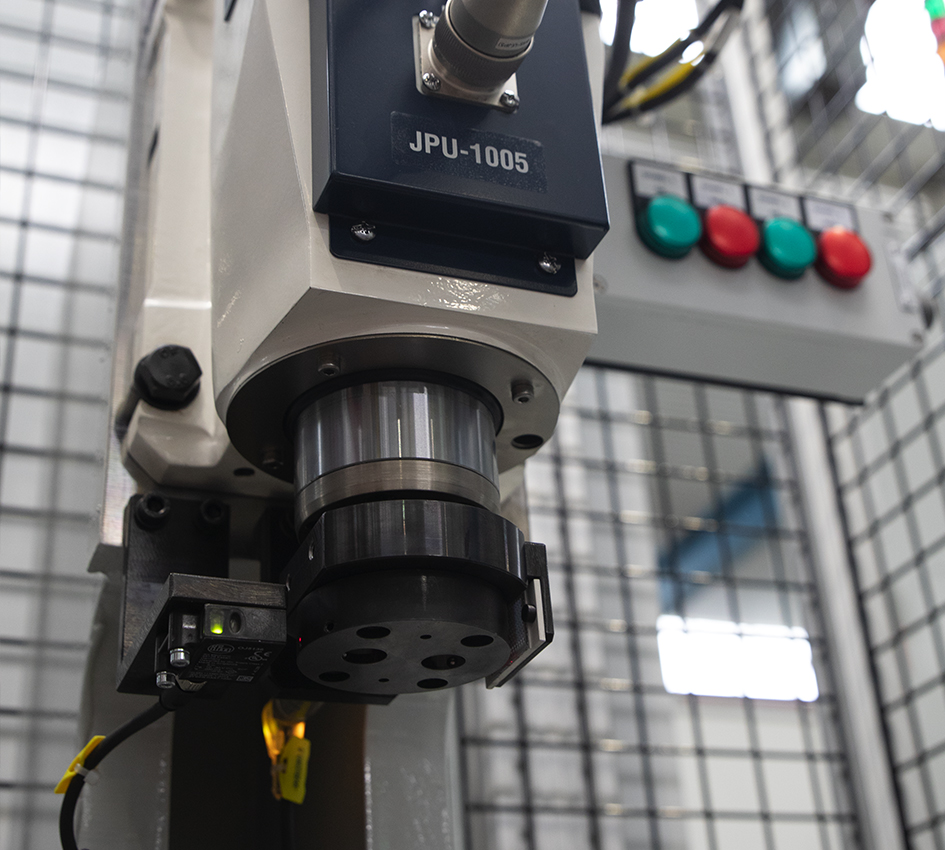
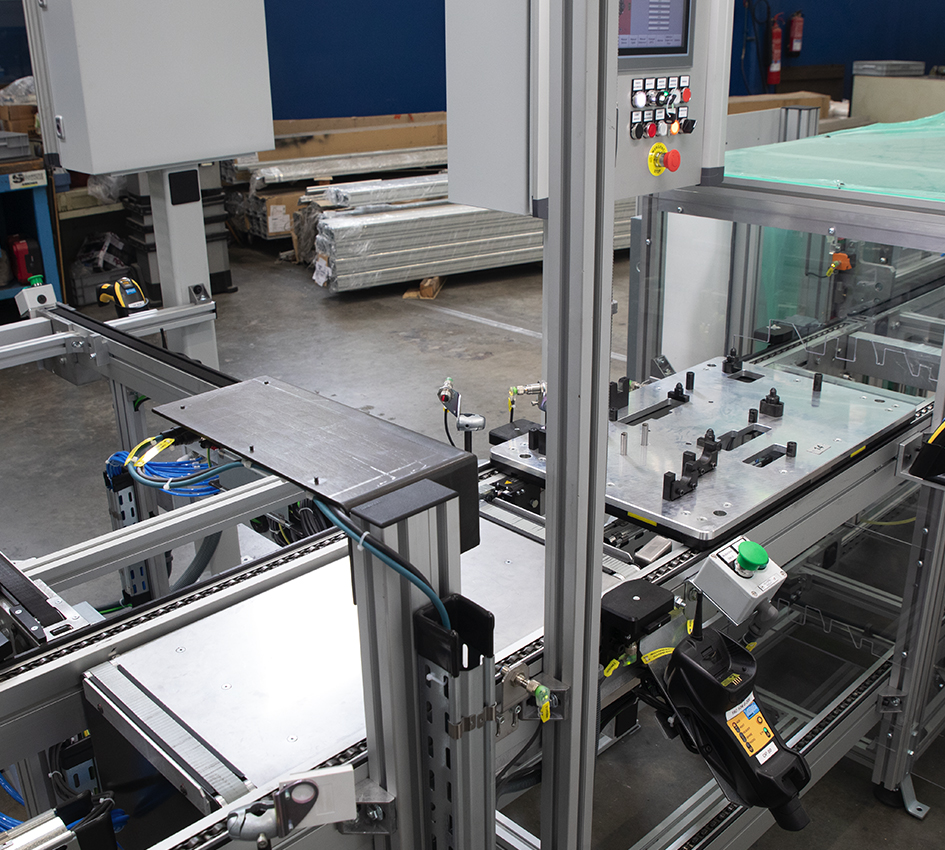
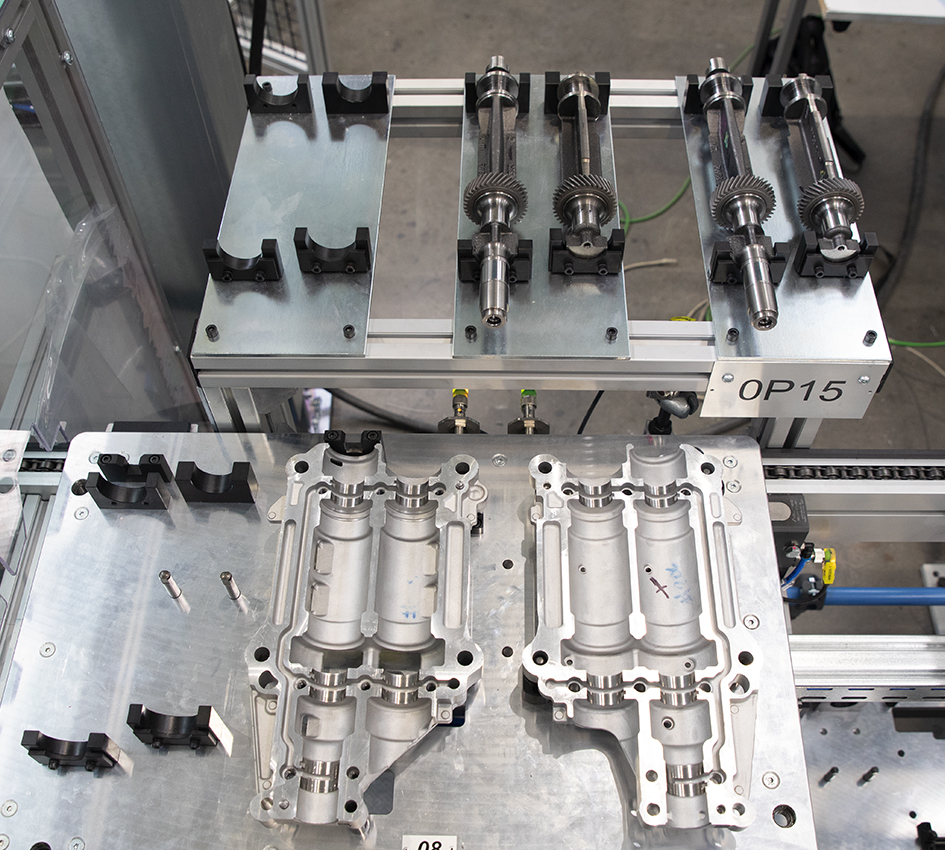
OPERATIONS
In-Line Stations | Assembly set loading to the pallet
At the first station on the palletized conveyor, the components to be assembled (housings and shafts) are loaded onto a pallet that will move the parts throughout the assembly line.
At this station, the 2D code on the housings and shafts is read by the operator using handheld scanners. This way, all components are linked to the 2D code marked in the previous operation, providing complete traceability of the assembled assembly.
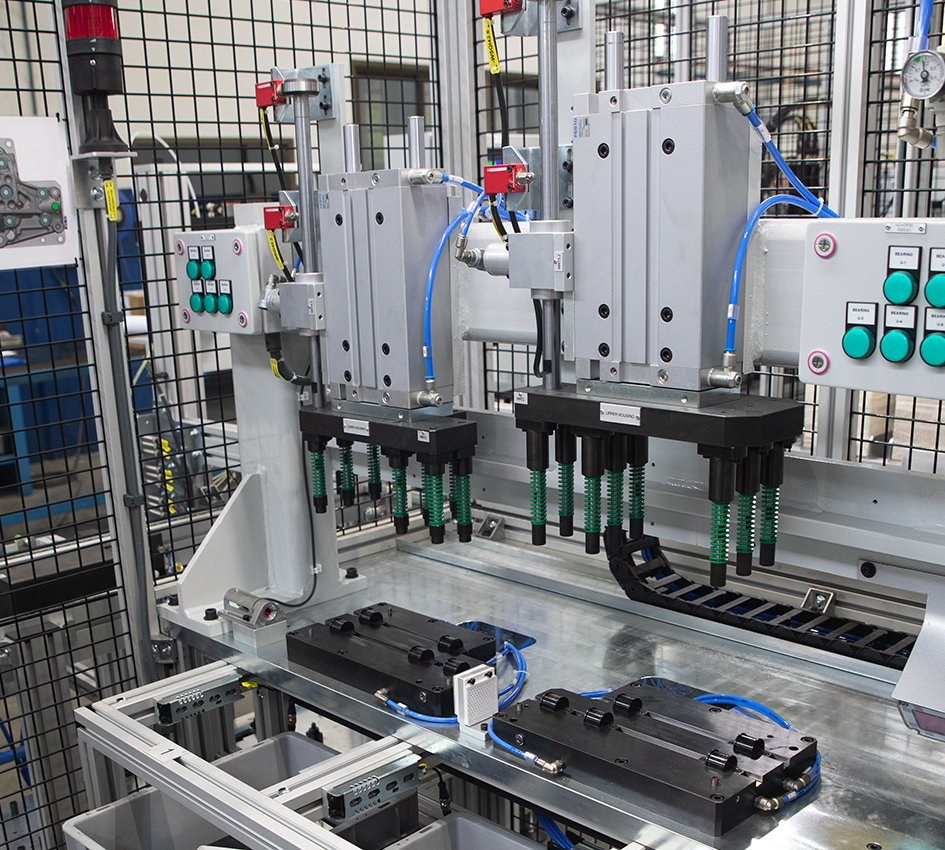
OPERATIONS
In-Line Stations | Bearing Assembly
3 different bearing models are assembled. The choice of bearing model is based on the dimensions of the shafts and housings indicated in the 2D codes of each component. To ensure the correct bearing is selected, each collection box will have a light-based selection system and manual passage detection.
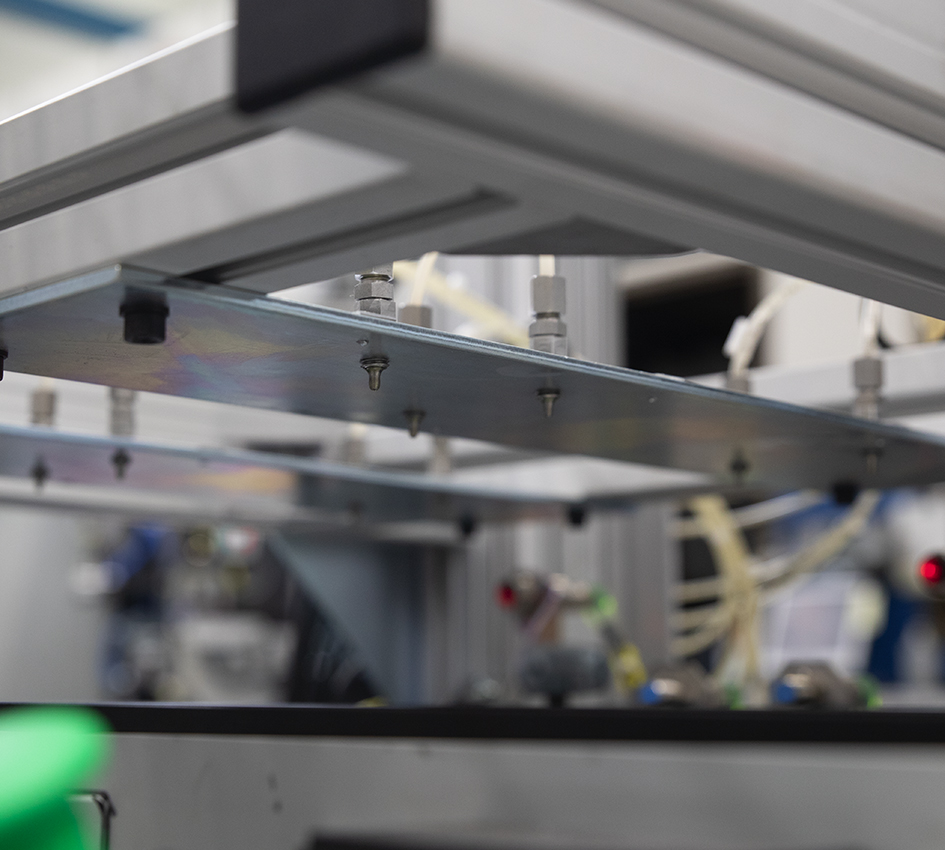
OPERATIONS
In-Line Stations | Oiling & shafts meshing and loading
At the first stop, the bearings are greased using automatic greasing nozzles. At the next stop, the operator engages the shafts and loads them into the housing.
A mechanical poka-yoke checks the correct angular position of the engaged shafts. Then, the operator places the upper housing onto the lower housing and manually feeds the bolts.
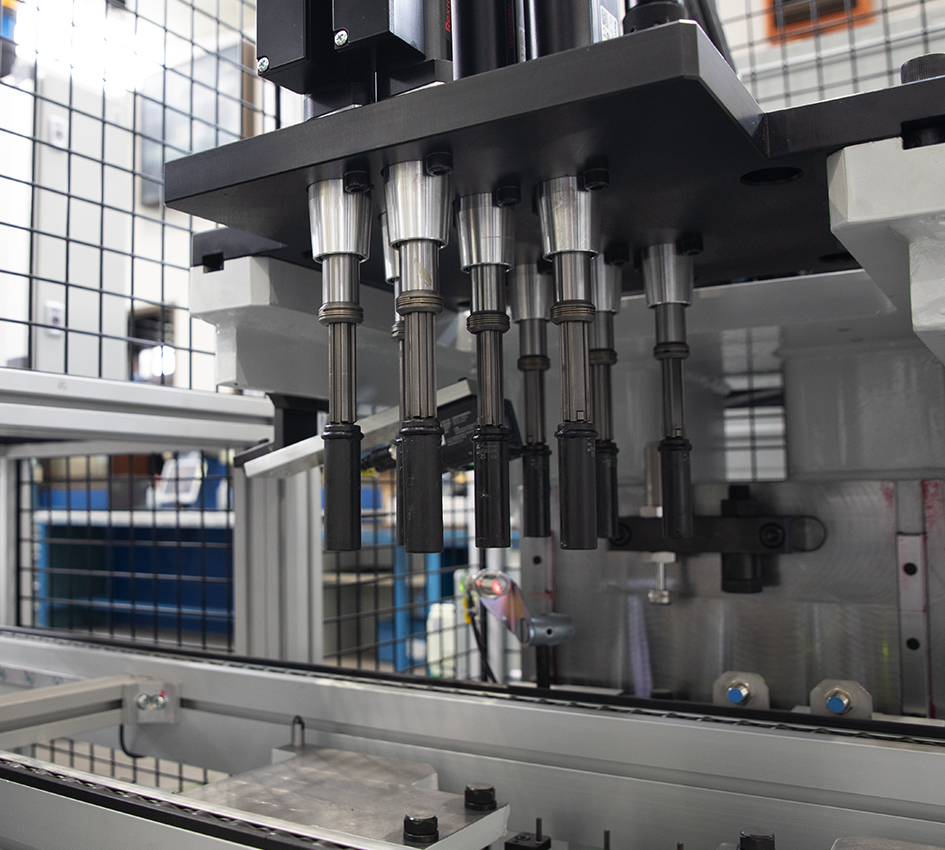
OPERATIONS
In-Line Stations | Automatic Bolts Tightening
The pallet arrives at the tightening station, and all bolts are tightened simultaneously using multiple torque-controlled spindles. One bolt is different (shorter) from the others, so the correct position of all bolts is monitored by sensors.
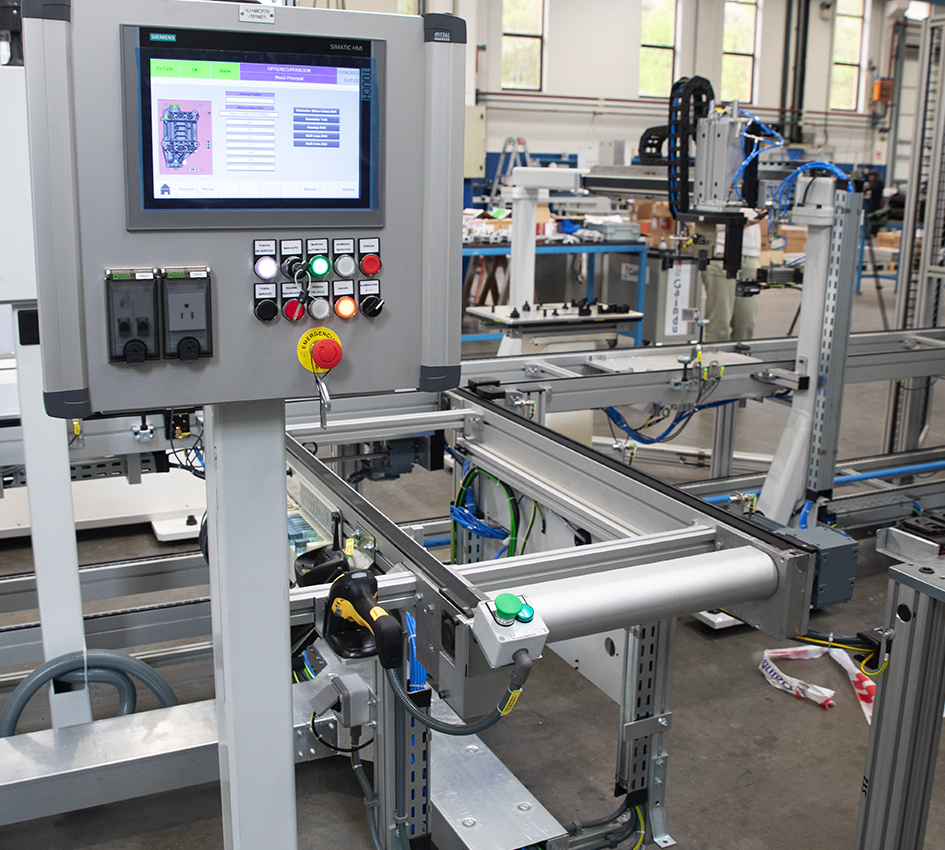
OPERATIONS
In-Line Stations | Rework Station
Before the final inspection, there is a camera to read the 2D code on the housing. If any of the previous operations were incorrect, the pallet is automatically moved to a reject conveyor. At the end of this reject conveyor, an HMI will display the reason for a part being NOK (not okay), and there will be a workstation to disassemble the entire housing.
Integrated technologies
DOWNLOAD CASE STUDYInterested in knowing more how we can help you?
CONTACT US