Leak testing
Leak testing is an important step in the validation of component quality in the automotive sector, medical technology, fittings technology and many other industries. Only through precise component testing can you be assured that your products are also functioning reliably.
How it works
Our Solutions
-
Unitary
- Small productions / Long cycle times.
- Small parts with simple leak test requirements.
- Manual or automated loading/unloading.
- No hydraulics. All the closures done with pneumatic cylinders.
- Plug and play design. Easy set up at destination.
- Easy maintainability and high reliability.
-
Rotary
- Highest testing accuracy that ensures the quality of the finished product.
- We offer our dial transfer machine with 4 or 6 stations with 1, 2 or 3 fixtures. Through this modular dial transfer design, our system will satisfy the required level of productivity for your specific application, thus allowing to optimize your investment.
- Its compact design saves floor space and allows for shipment in 1 pack.
- Highest testing productivity, through simultaneous working stations.
- Flexibility to run different part types.
- Easy accesibility to the clamping fixtures.
- Easy maintainability and high reliability.
- Engineered and customized solutions.
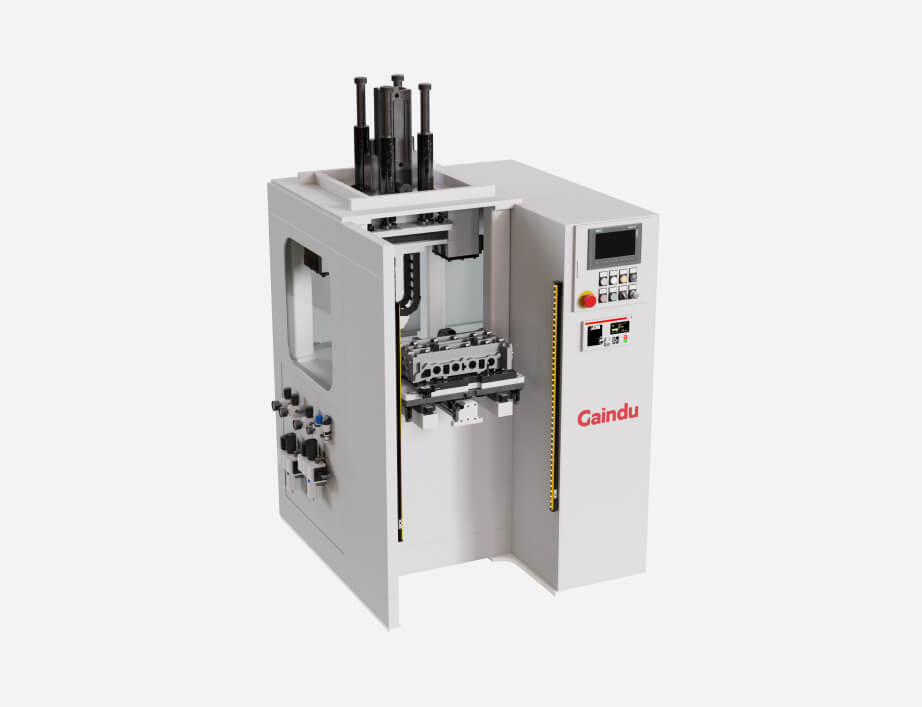
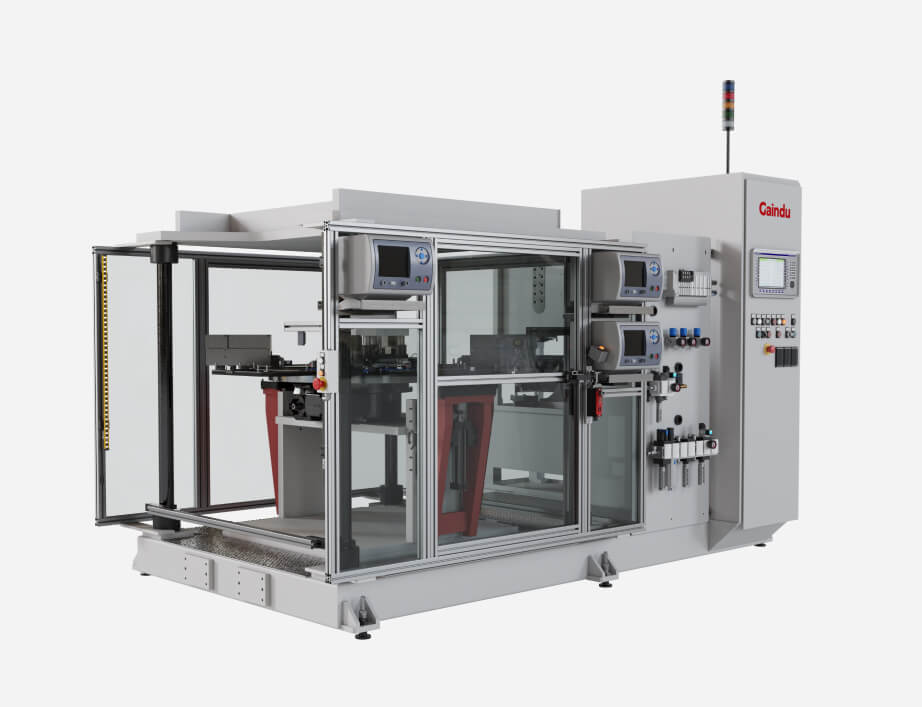
Features
MODULARITY
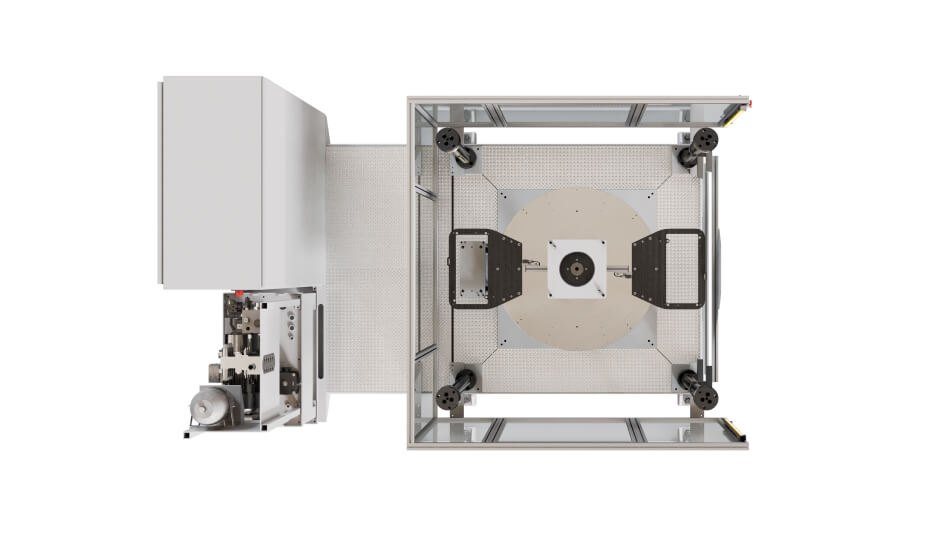
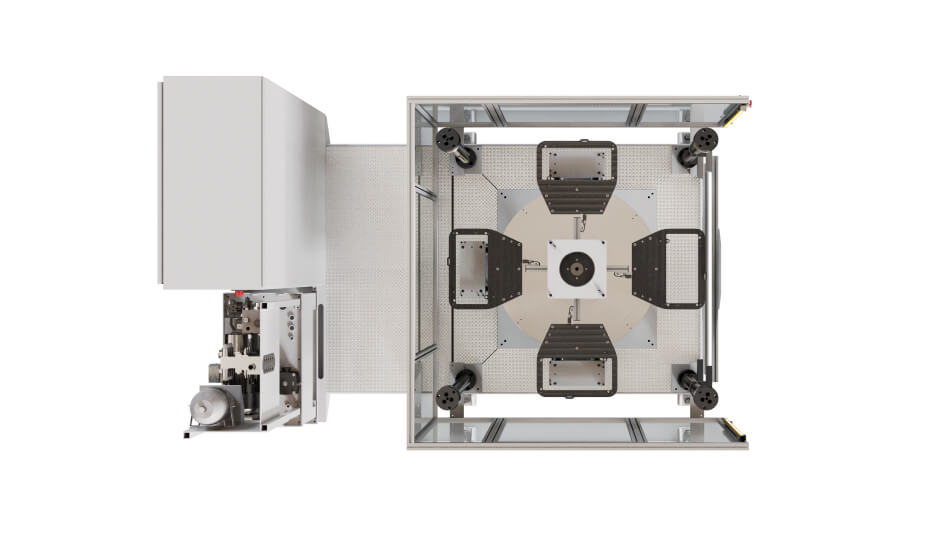
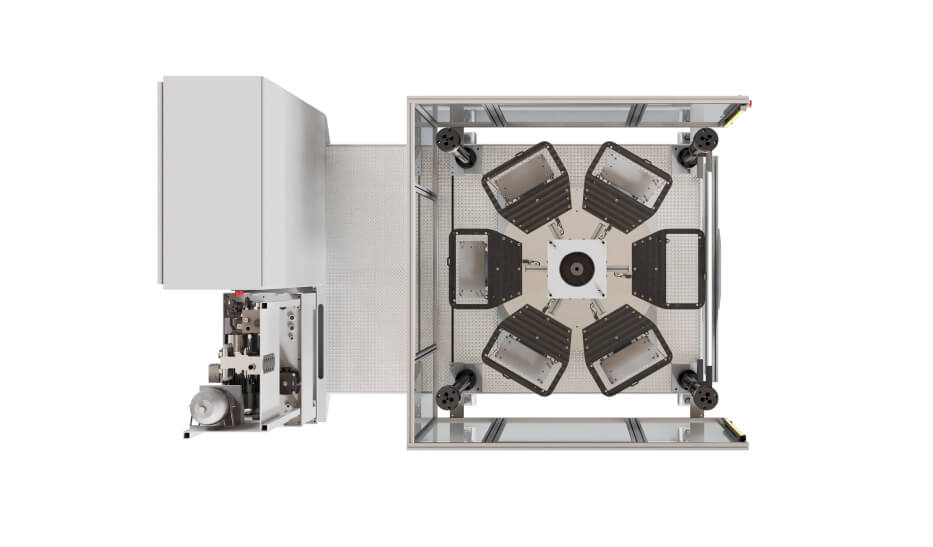
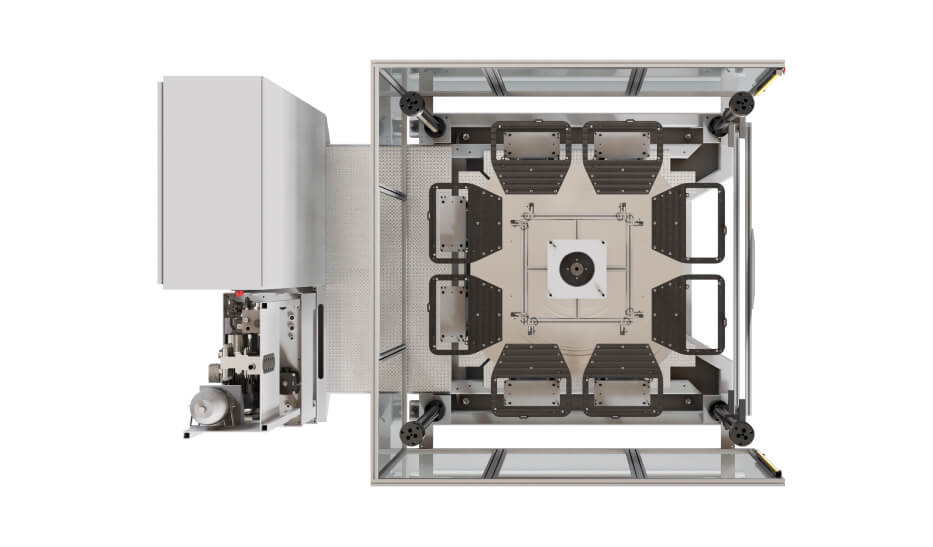
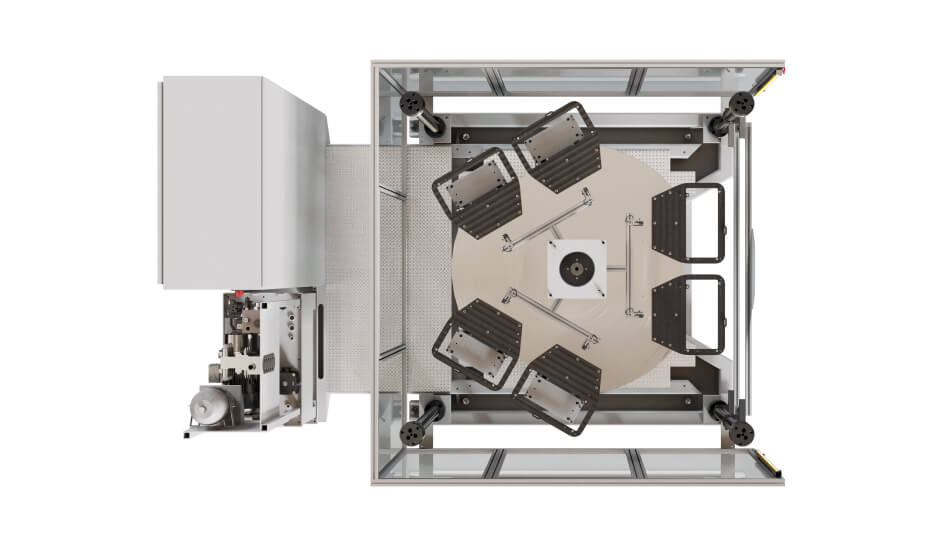
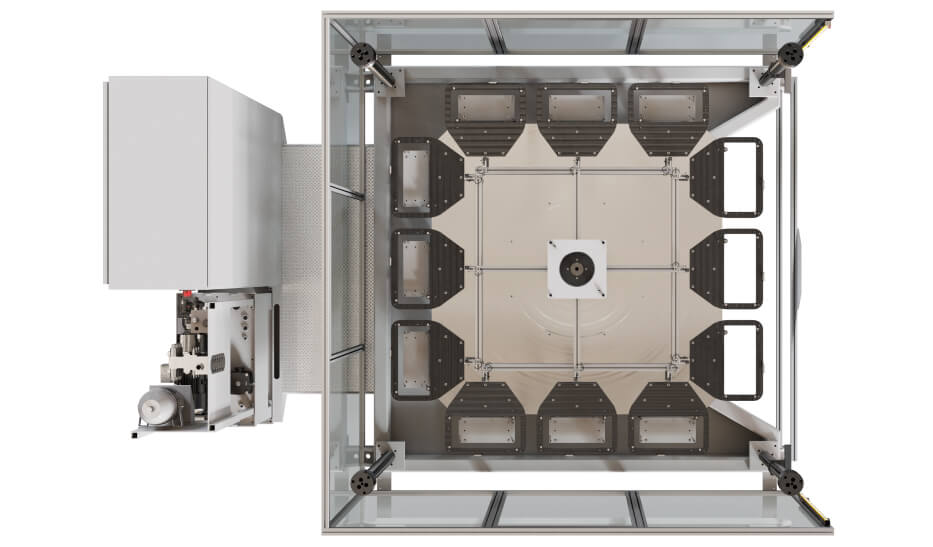
FLEXIBILITY
For high production rates, our quick change clamping fixtures allow for fast and reliable changeover, in manual or automatic mode.
The LEAKflex series provides optimum flexibility for a broad spectrum of parts including, cylinder blocks, cylinder heads and transmission components, in a variety of sizes and seals.
For lower volumes, we can tool our 4 or 6 stations for different part types and obtain automatic changeover with zero mistakes, performing multiple checks at each individual station.
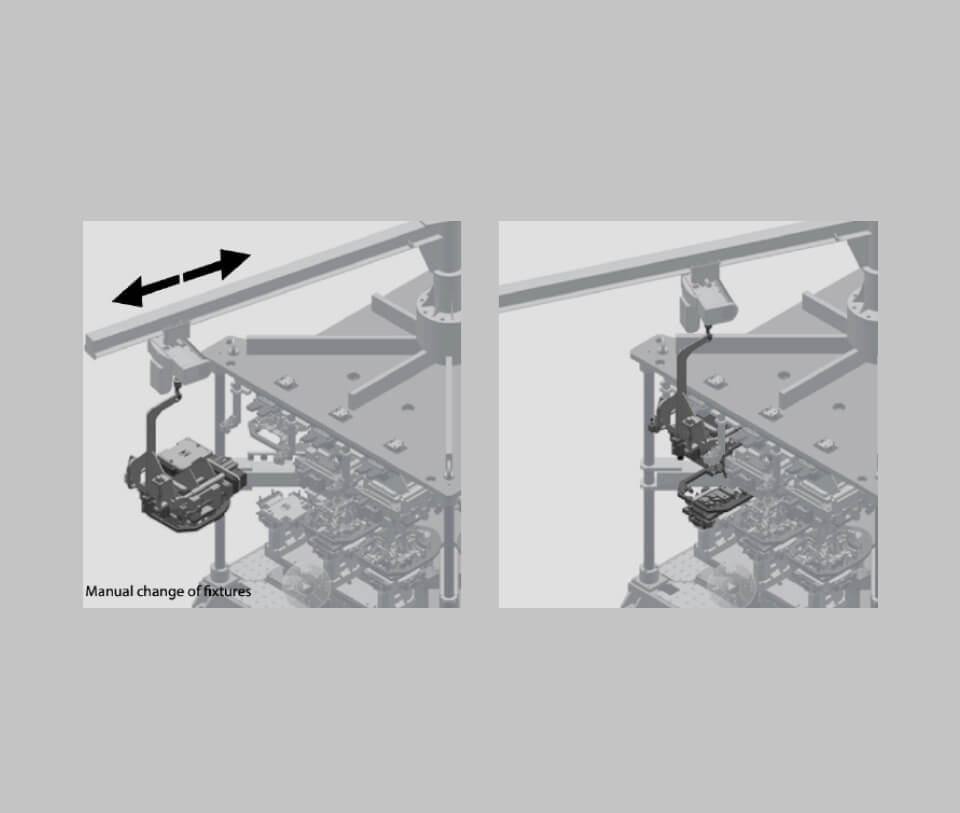

Technologies
-
Automation Technologies
We offer integral solutions to optimize the productivity, being the automation of the loading/unloading and feeding of parts to the production systems a fundamental part of this process.
-
Traceability Technologies
Our cells include the means to completely trace the parts and ensure that the information is recorded for further processing. Some of the technologies used for this purpose include marking, reading and data storage.
-
Testing Technologies
Quality assurance in our products and therefore in our customer's final product is an absolute priority for us. In this direction we work to offer the best quality control systems in different areas.
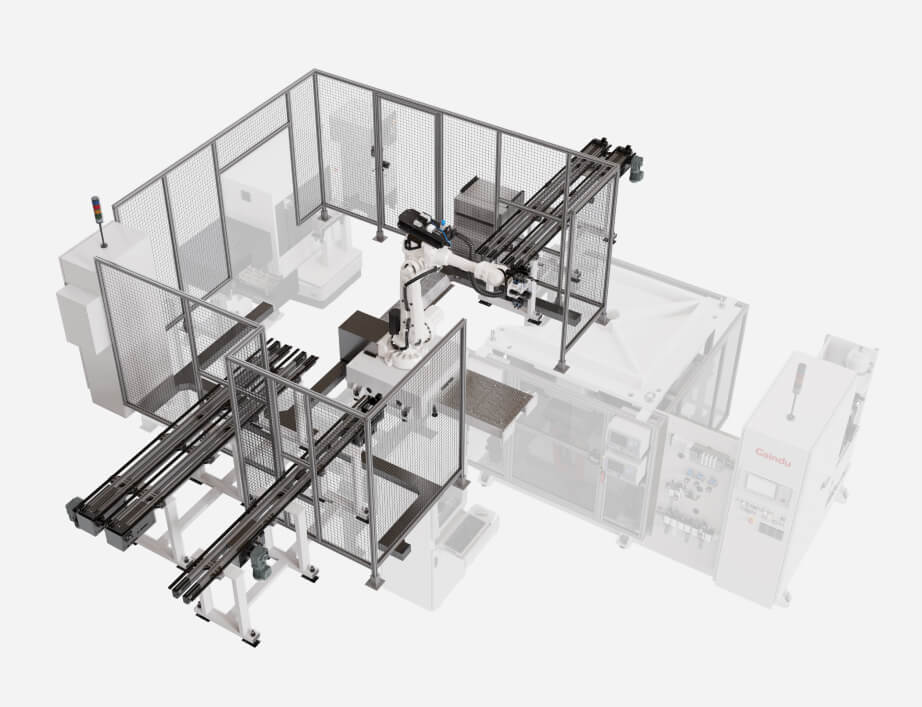
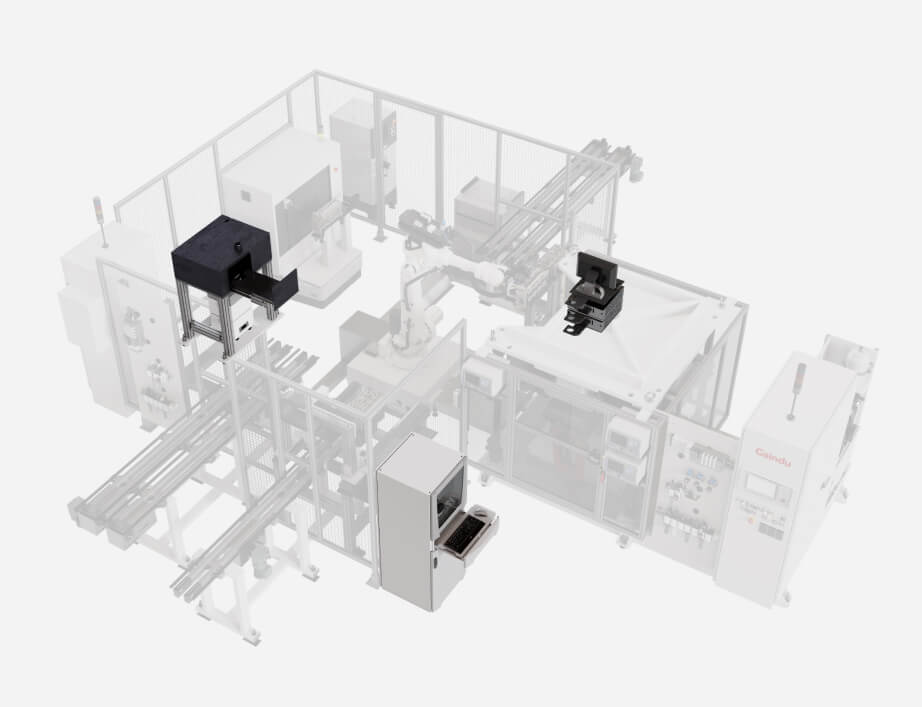
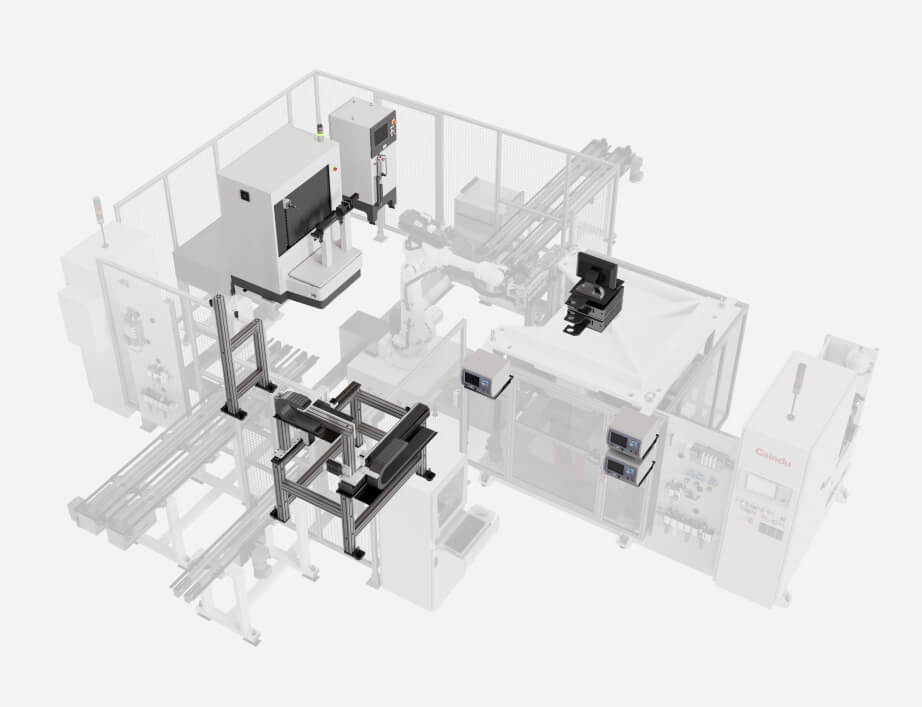
Applications
-
CYLINDER BLOCKS
- Water Jacket
- Crankcase
- Oil gallery
- Secondary air passages
-
TRANSMISION HOUSING
- Main cavities
- HP Oil Channels
- Power Electrocnics
-
TRANSMISION HOUSING
- Main cavities
- HP Oil Channels
- Power Electrocnics
-
CYLINDER HEADS
- Water Jacket
- Spring deck
- High Pressure
- Oil gallery Intake / Exhaust ports
- Oil drain
- EGR coolant passage
- Flow operations
-
BATTERY BOX
- Main cavities
Case studies
Gaindu has collaborated to improve their production processes or undertake complex operations in an efficient way.
MORE ABOUT CASE STUDIESInterested in knowing more how we can help you?
CONTACT US