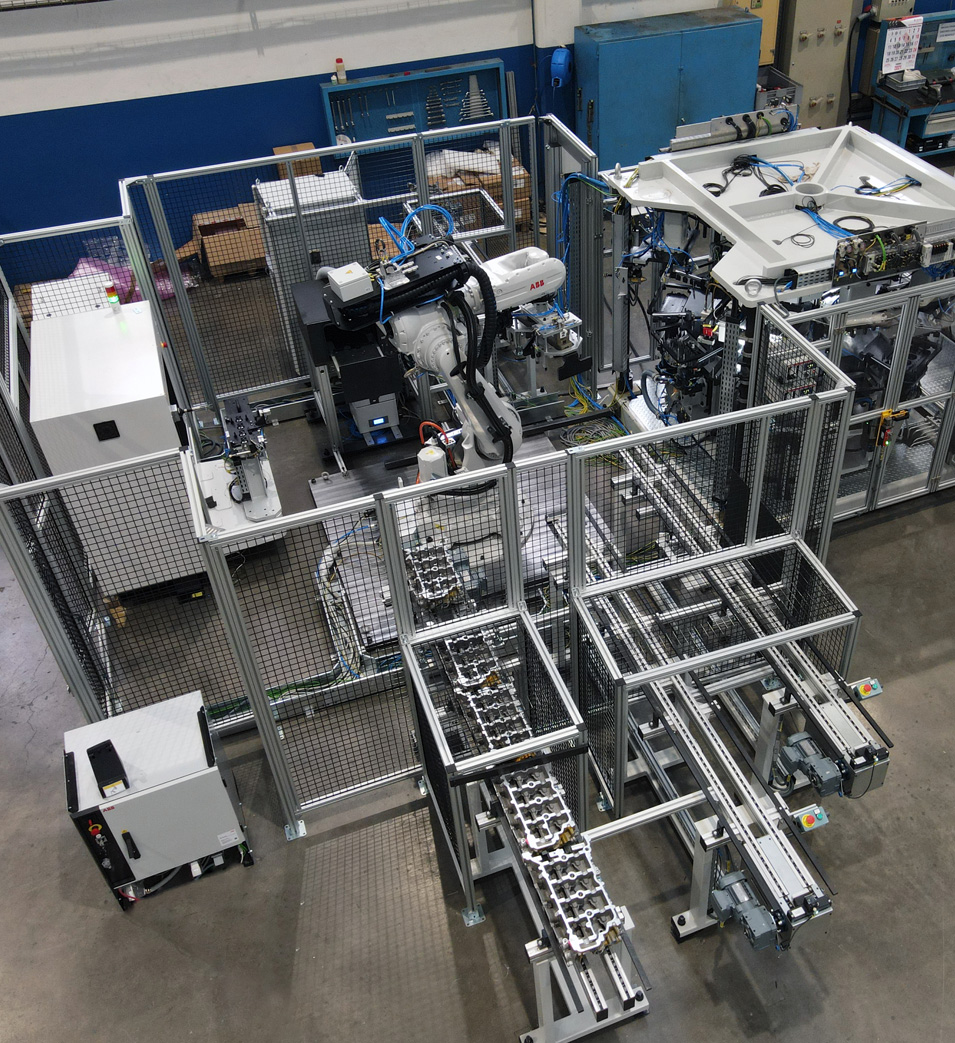
Challenger
In order to be able to integrate all the tests of all the required galleries, the project was carried out using as a basis our standard leak test machine in 9 stations format (8 working stations and 1 loading/unloading station).
On the loading/unloading station it was included the possibility to check the correct state of the water gallery, checking the presence of the different orifices on the combustion face of the piece. The overall application was completed with a laser marking system integrated into the robotic cell and with the integration of a CMM measuring machine for checking the dimensional dimensions of the part.
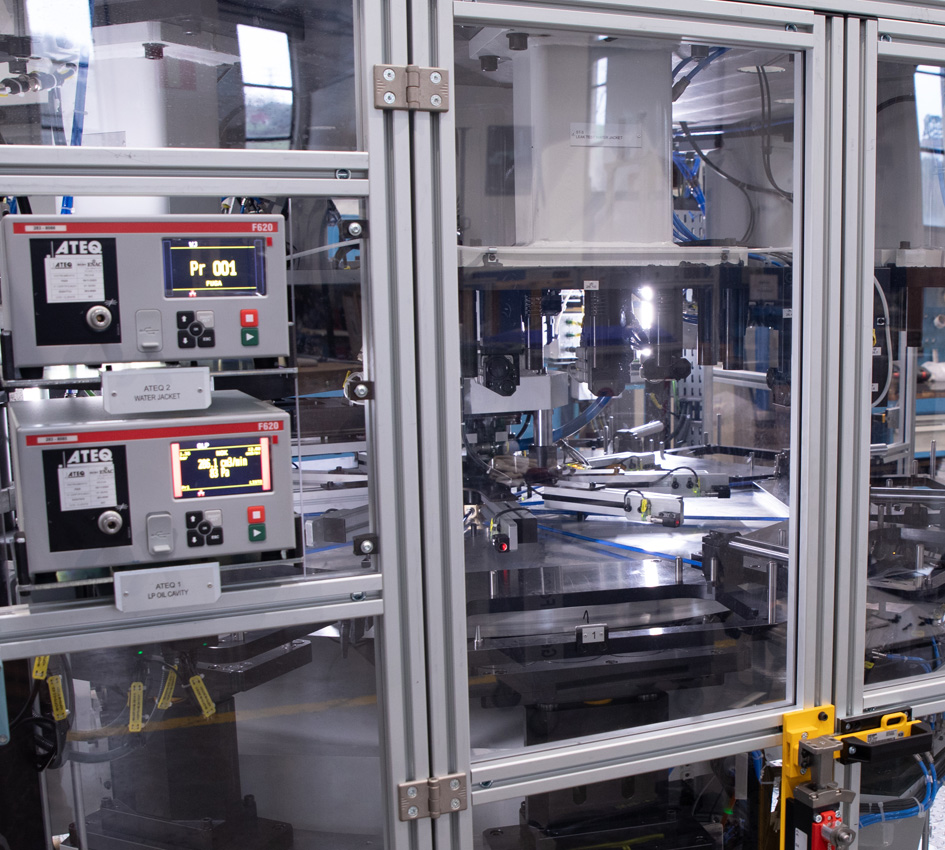
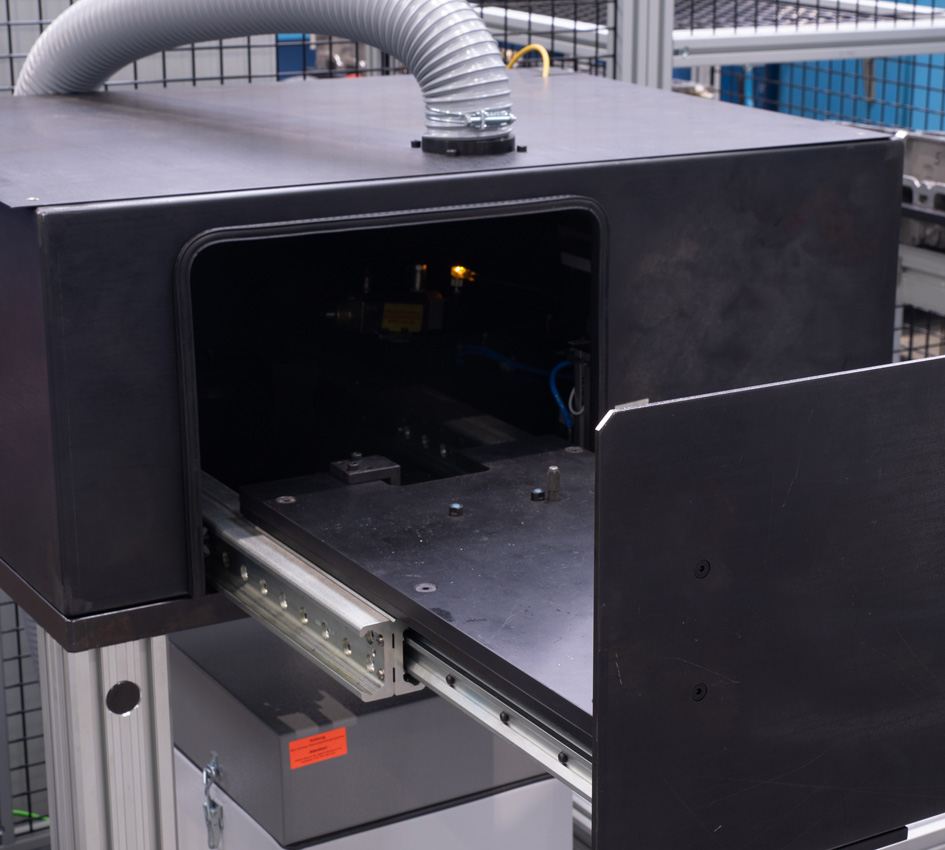
OPERATIONS
Marking
Inside the robotic cell, a laser part marking station was included, with a Class 4 laser protection solution designed exclusively for the project part. The equipment includes a fume and particle aspiration equipment generated in the process, as well as the reading by means of a vision camera to check the correct marking (including reading grade definition).
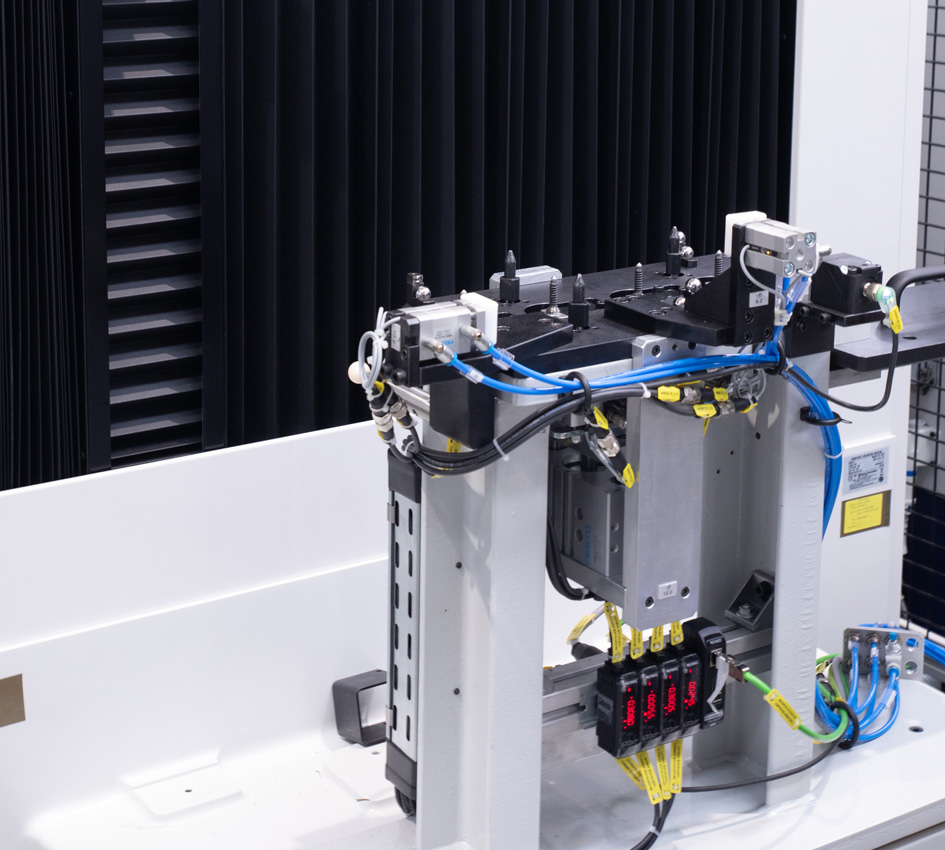
OPERATIONS
Measuring
Measurement of more than 10 dimensional references of the part, using a Mitutoyo CMM machine that we integrate inside the cell, referencing the part over a mechanical fixture of Gaindu's own design.
In this way we provide the leak test control cell with additional quality control tools to be able to ensure, on the same installation, the requirements demanded by the end customer of the project.
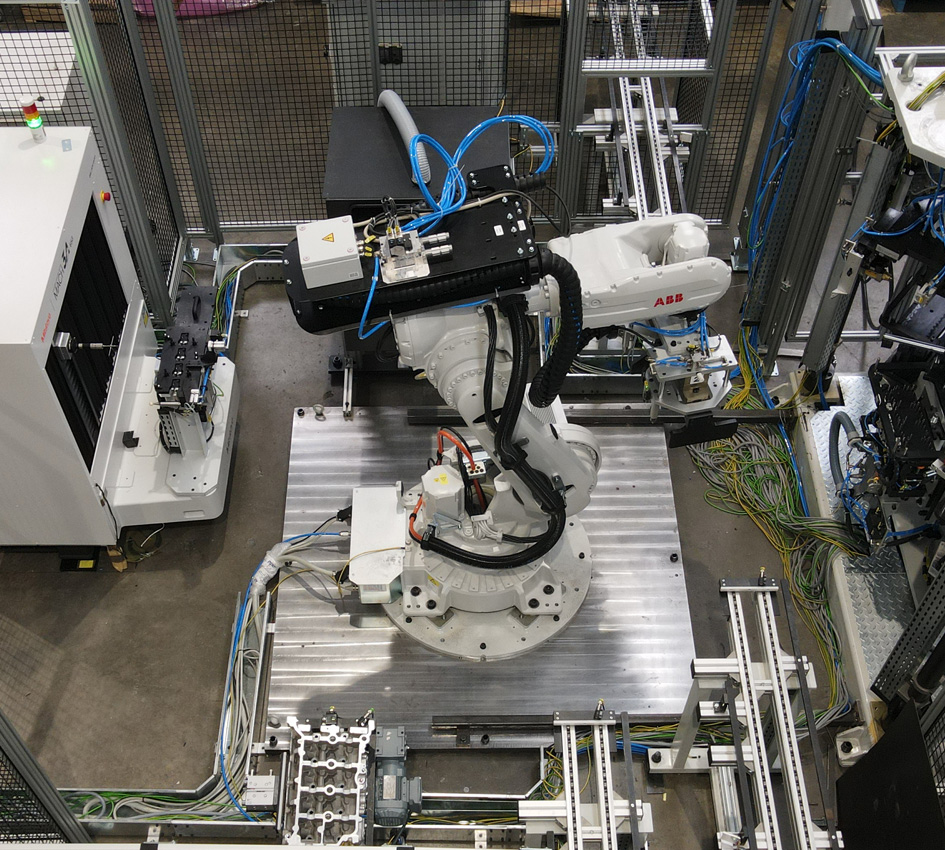
OPERATIONS
Robotized cell
The productivity of the cell is enhanced by the automation of the loading/unloading of the leak test machine and the various peripheral stations. In the same way, the input/output conveyors are integrated to the cell in order to obtain an automatic buffer independent of the operator's presence on the equipment.
Integrated technologies
Interested in knowing more how we can help you?
CONTACT US