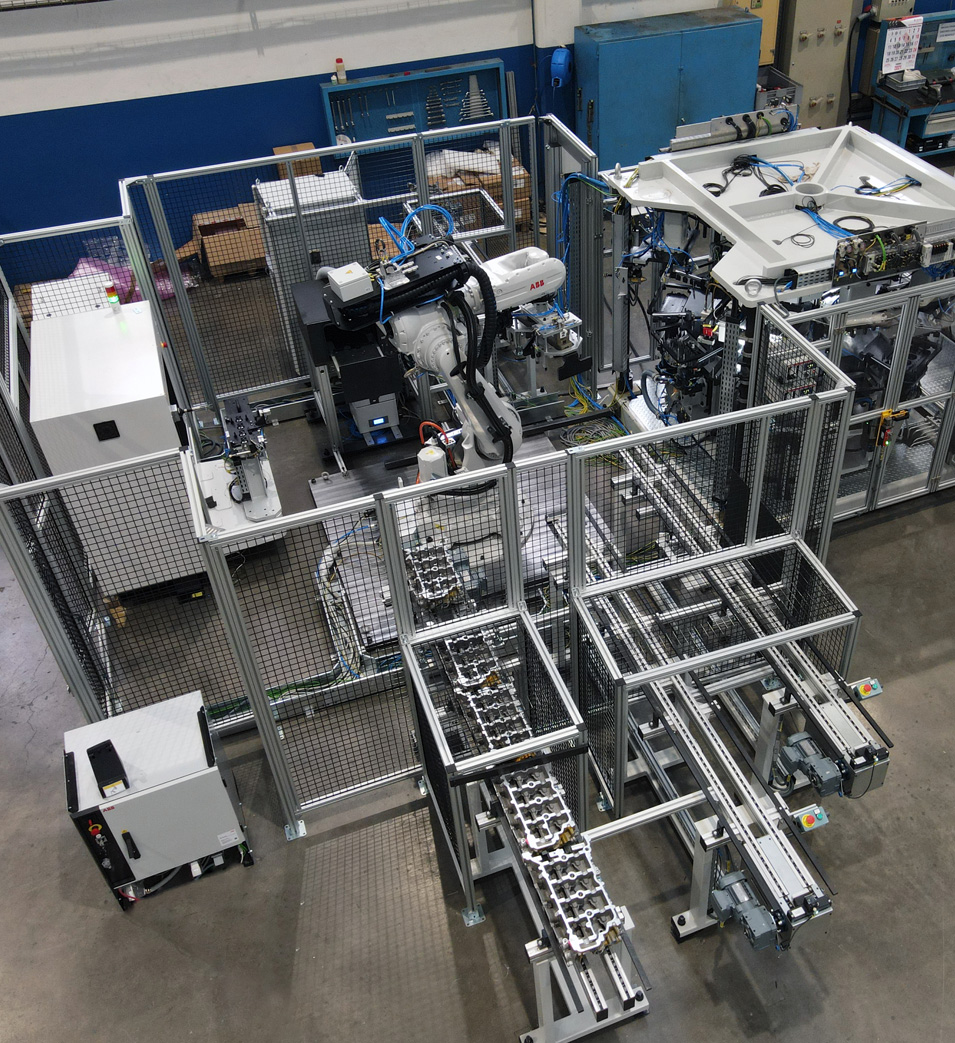
Herausforderung
Um alle Tests aller erforderlichen Stollen zu integrieren, wurde das Projekt mit unserer Standard-Dichtheitsprüfmaschine im 9-Stationen-Format als Basis durchgeführt (8 Arbeitsstationen und 1 Be-/Entladestation).
In der Be-/Entladestation wurde die Option integriert, den korrekten Zustand des Wasserkanals zu überprüfen und das Vorhandensein der verschiedenen Löcher auf der Verbrennungsfläche des Teils zu prüfen. Die weltweite Anwendung wurde durch ein in die Roboterzelle integriertes Lasermarkiersystem und die Integration einer KMG-Messmaschine zur Überprüfung der Werkstückabmessungen vervollständigt.
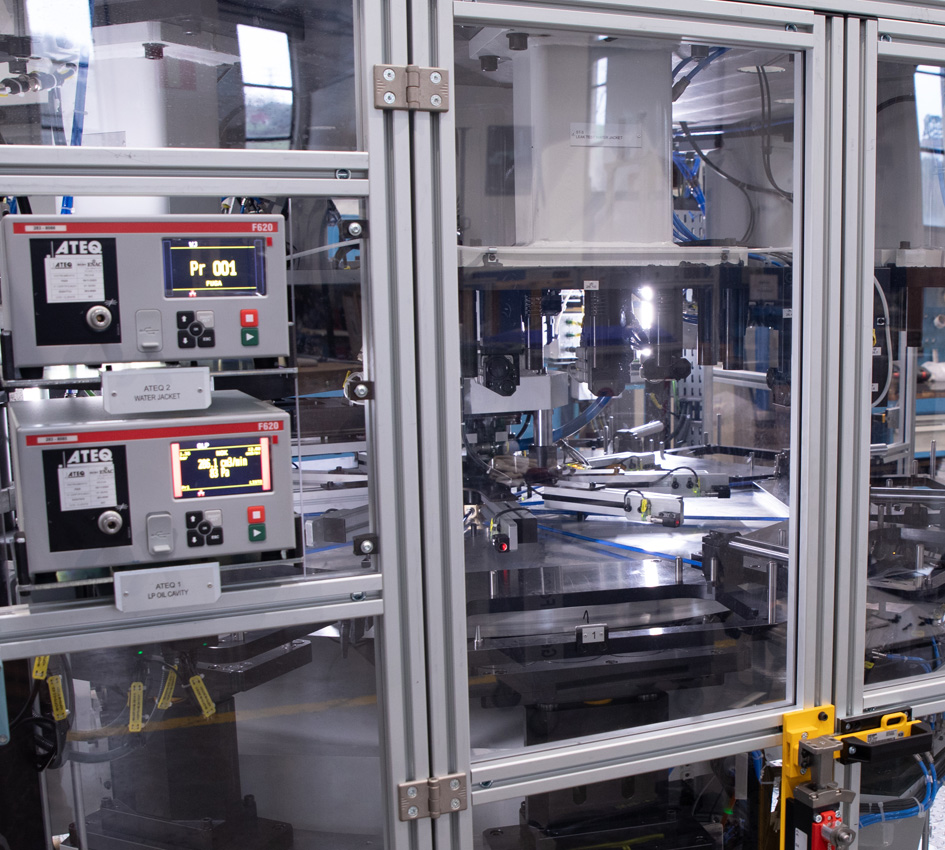
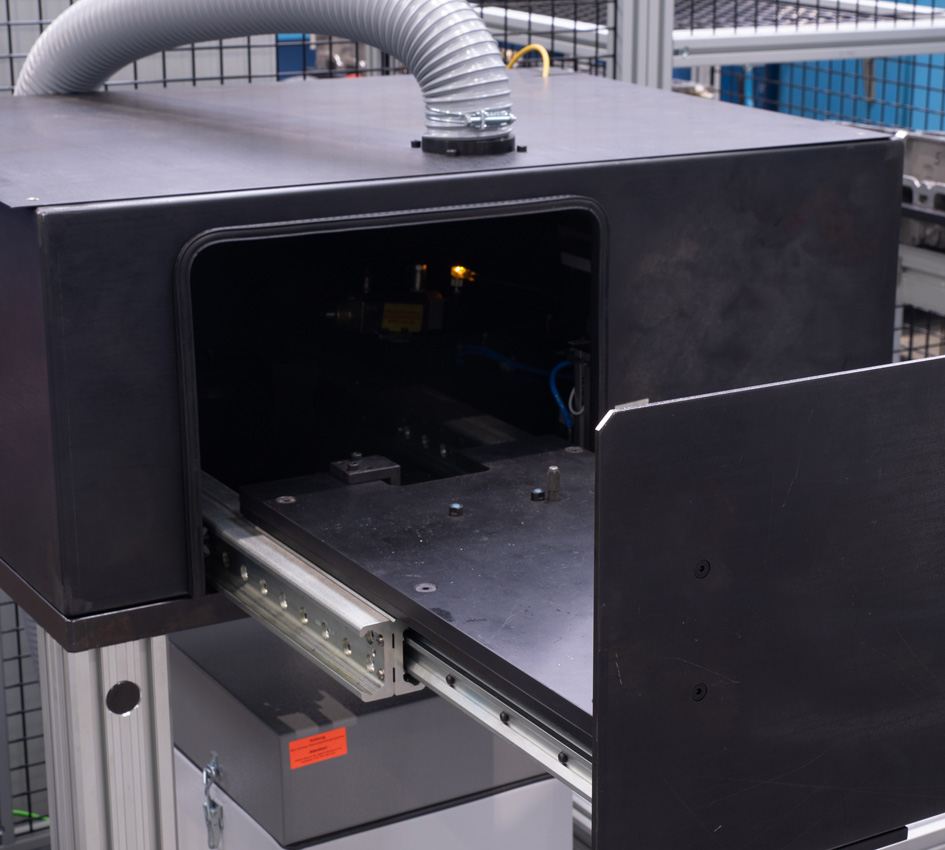
ARBEITSFOLGEN
Kennzeichnung
In die Roboterzelle wurde eine Laser-Teilemarkierungsstation integriert, mit einer Laserschutzlösung der Klasse 4, die ausschließlich für das Projektteil entwickelt wurde. Zur Ausstattung gehören eine dabei entstehende Rauch- und Partikelabsaugung sowie die Lesung mittels Vision-Kamera zur Überprüfung der korrekten Kennzeichnung (einschließlich der Definition der Lesestufe).
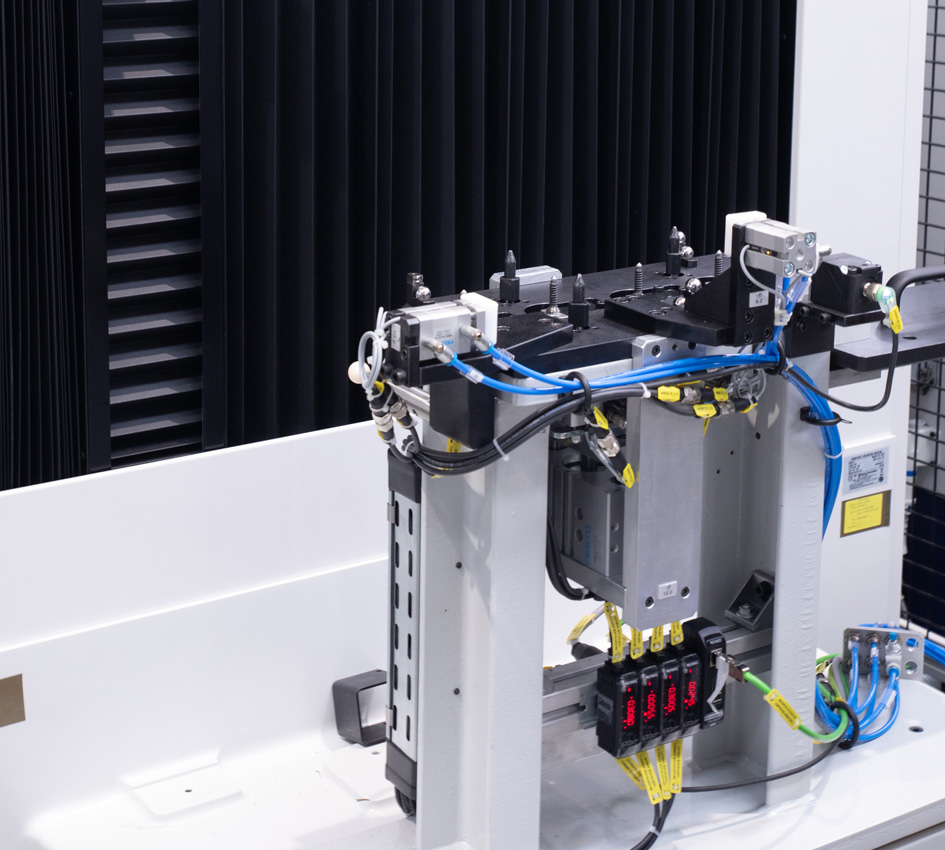
ARBEITSFOLGEN
Messung
Messung von mehr als 10 Größenreferenzen des Werkstücks mit einer Mitutoyo CMM-Maschine, die wir in die Zelle einbauen, wobei das Werkstück auf einem mechanischen Werkzeug im eigenen Design von Gaindu referenziert wird.
Auf diese Weise statten wir die Dichtheitskontrollzelle mit zusätzlichen Qualitätskontrollinstrumenten aus, um in derselben Anlage die vom Endkunden des Projekts geforderten Anforderungen gewährleisten zu können.
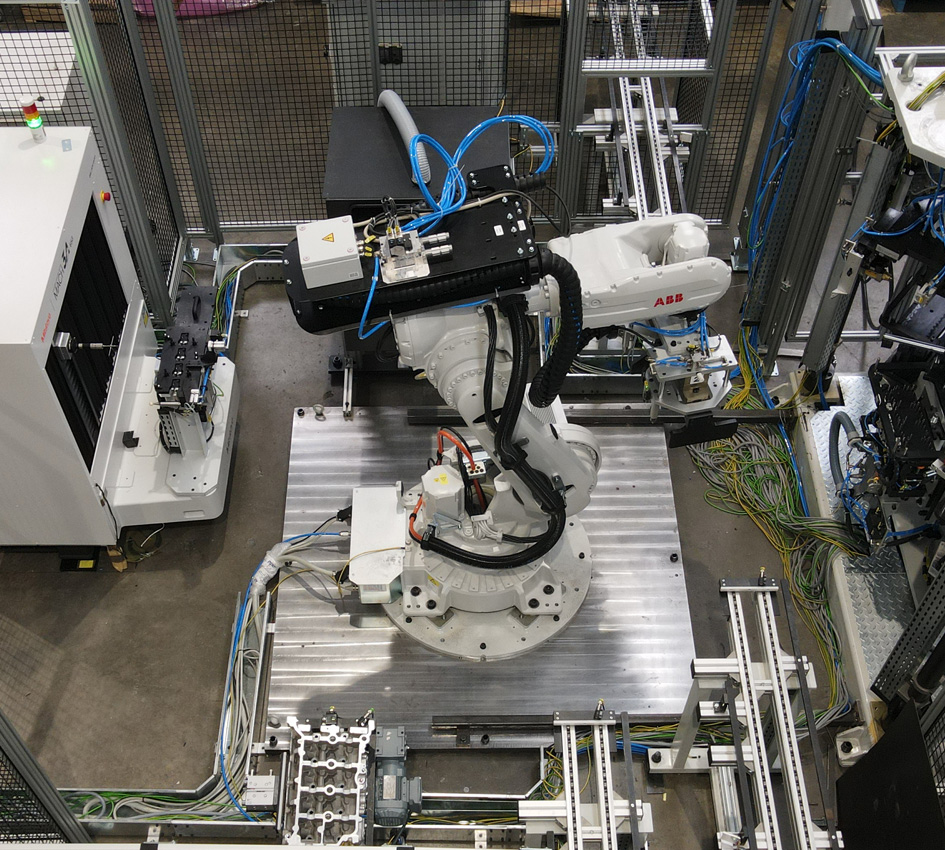
ARBEITSFOLGEN
Robotisierte Zelle
Die Produktivität der Zelle wird durch die Automatisierung der Be- und Entladung der Dichtheitsprüfmaschine und der verschiedenen Peripheriestationen gesteigert. Auf die gleiche Weise werden die Eingangs-/Ausgangsförderer in die Zelle eingebaut, um einen automatischen Puffer unabhängig von der Anwesenheit des Bedieners in der Anlage zu erhalten.
Integrierte Technologien
Möchten Sie mehr darüber erfahren, wie wir Sie unterstützen können?
KONTAKTIEREN SIE UNS