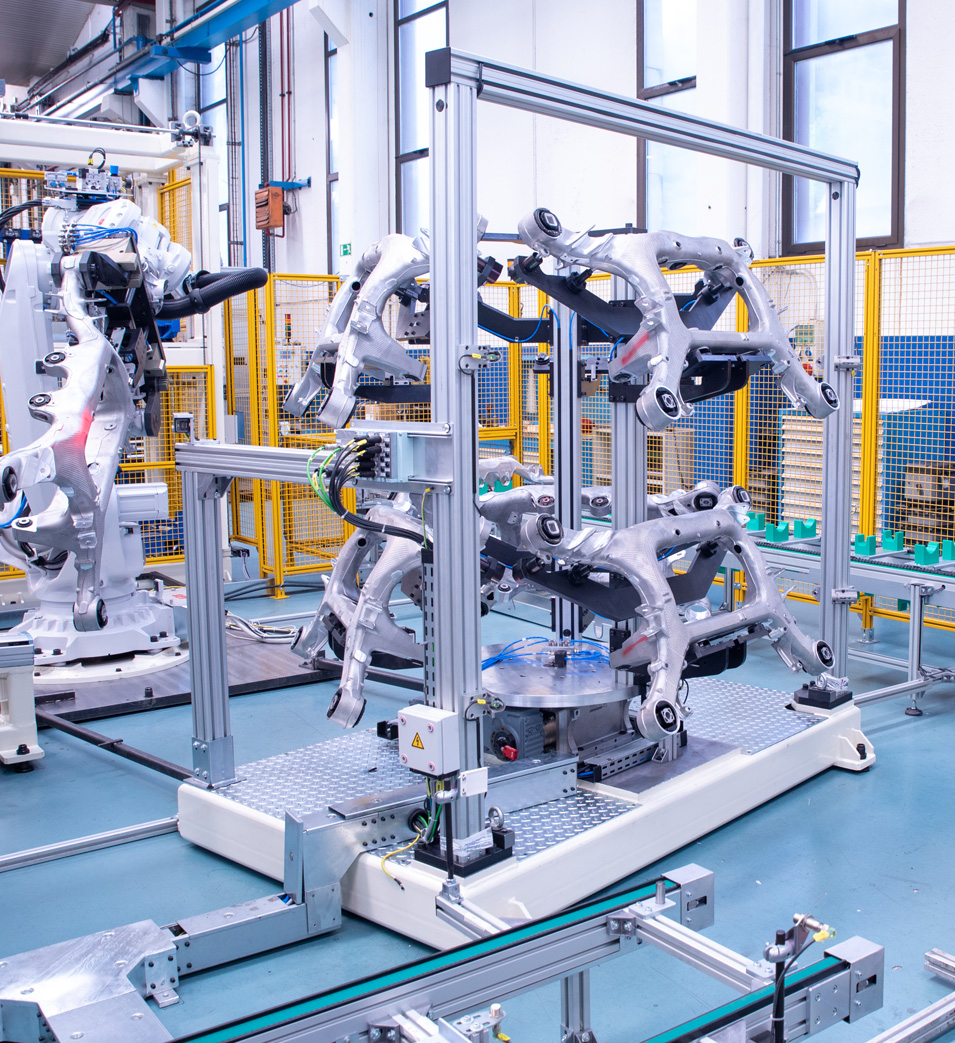
Challenger
From the outset, the project represented a unique opportunity to apply our flexible assembly machine concept to the production of a large and complex structural part.
The customer's requirements in terms of component orientation, as well as the variety of assembly angles needed, made our Flexible Bushing Assembly machine a perfect fit for the project's needs. The application consists of assembling 9 components on an aluminum casting subframe, with a total of 10 different types of components.
Prior to the assembly, a recognition of the types of components and their angular orientation is performed (using artificial vision equipment), in order to guarantee their correct assembly following the drawing specifications.
The complete automated cell includes 3 loading/unloading robots, automatic feeding units and the complete traceability management from the input of the machined part to the output (over the shipment rack) assembled, marked and inspected.

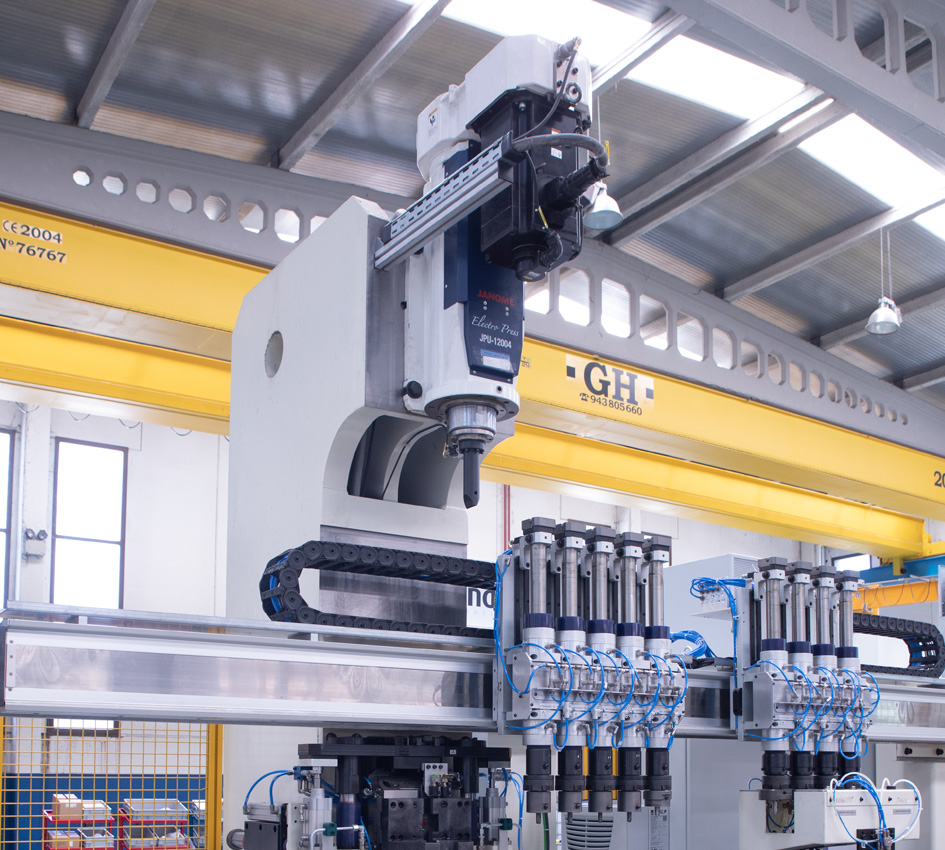
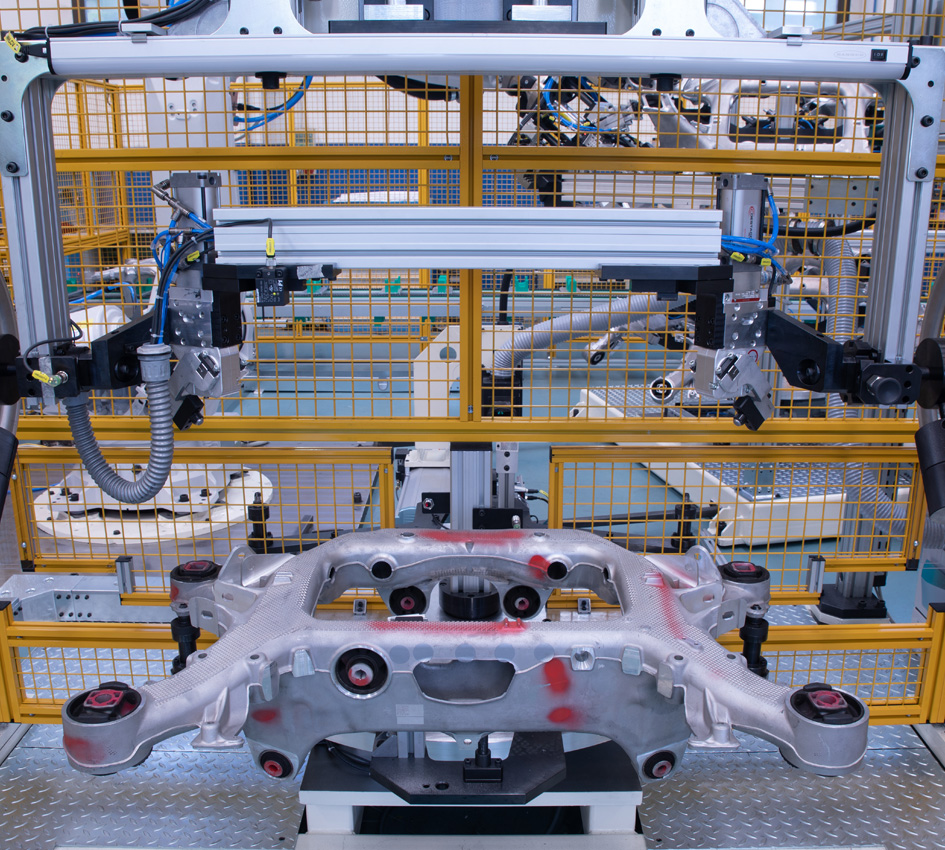
OPERATIONS
Marking and inspection
After the assembly process, the part is marked by means of a laser marking equipment, after which the correct marking is checked by means of a vision system.
Once marked, the part is extracted using a turning table on a free turning unit, to be evaluated by visual inspection for possible casting / machining defects. After the inspection operation, the part is returned to the cell.
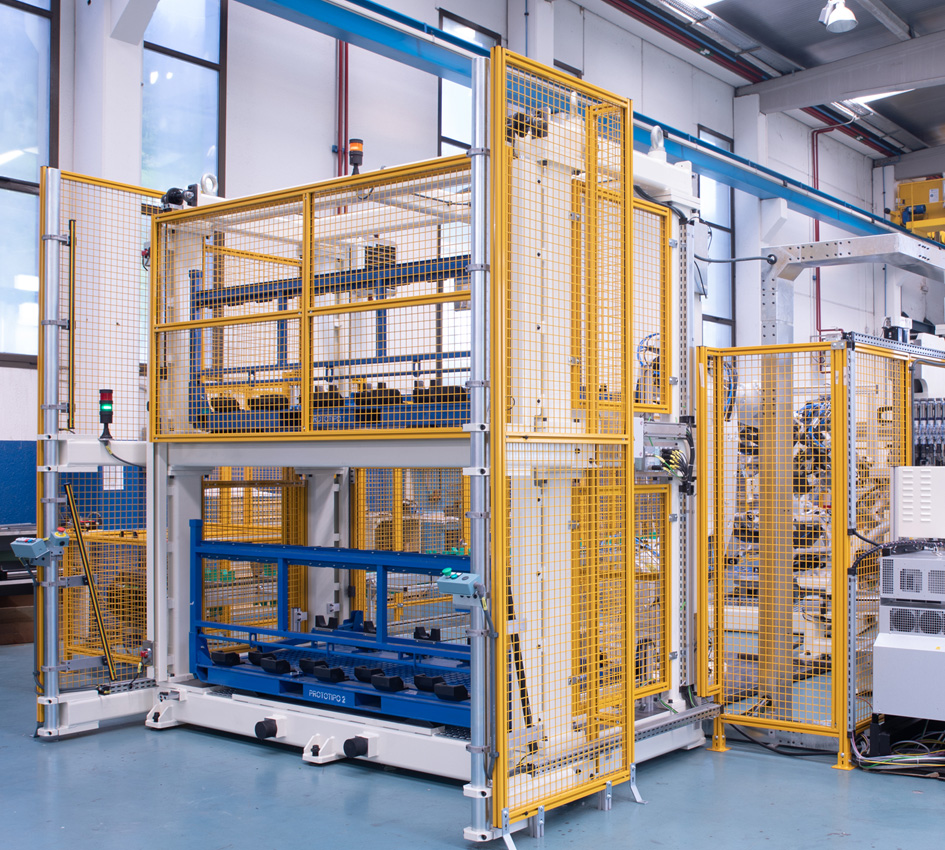
OPERATIONS
Palletizing
Once the part is completely assembled, marked with the corresponding process data and inspected by the line operator, it is unloaded by robot onto the end customer's racks.
The system allows the change of containers on the outside of the cell without interrupting production, maintaining cell productivity.
Integrated technologies
Pressing
- Monitoring of the assembly processes for component pressing, controlling the parameters during the whole cycle.
- At Gaindu we have installed more than 300 electric presses with which we have assembled all types of parts and units. Assembly processing of engines, suspensions, gearboxes, etc...
- We are the official distributor of JANOME electric presses in Spain, having collaborated with them directly in the validation and expansion of assembly processes using electric presses.
- Following our vocation of customer-oriented solutions, we adapt to the approved brands and preferences of our customers when designing our installations. This has led us to work with the leading global manufacturers of electrical presses and gives us the advantage of being able to offer our solutions integrating reliably any of these brands.
TRADEMARKS
Robot
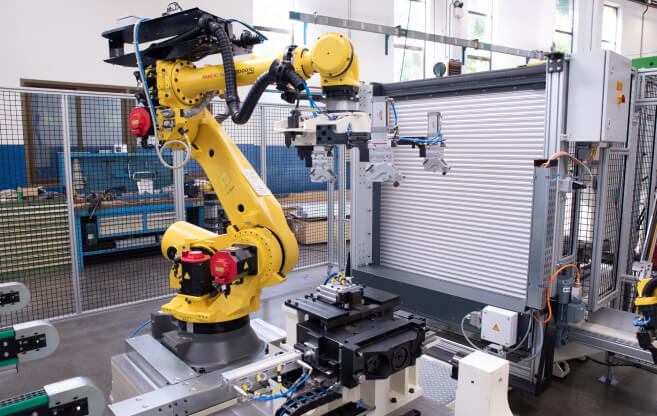
- When talking about automatic loading / unloading of our machines, integration of six axes and cartesian robots becomes a guarantee for high efficiency solutions.
- We have wide experience in integrating robots of various brands, not only for handling purposes but also as a key tool in some of our assembly standarized solutions.
- Design and integration of in-house designed grippers (EOAT), adapted to the needs of each application.
- Simulation services for the entire robot cycle to assure the process in cycle time conditions and to avoid possible collisions or interferences.
TRADEMARKS
Feeding
- When it comes to automating processes, automatic component feeding is a fundamental aspect of the cell's autonomy.
- There are several alternatives on the market to automatically feed parts to be assembled. At Gaindu we analyze each case individually to offer the best alternative, taking into account key aspects such as speed, part protection or required orientation.
- Among the alternatives we work with, we make our own design feeders by means of vertical warehouses as well as bowl-feeder or step-feeder integrations, which we customize for each application.
TRADEMARKS
Gaindu Tracker
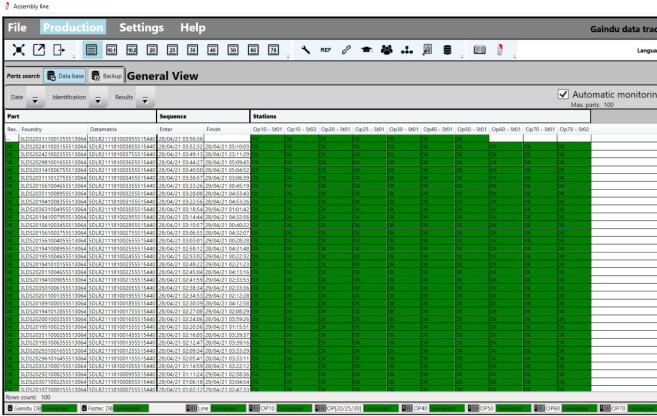
In order to respond to the traceability needs of our customers, at Gaindu we have developed our own software called Gaindu Tracker, with which we provide our installations with the functionality to record process data associated with unique part IDs.
We integrate industrial PCs from leading manufacturers as hardware support for our customized software development.
Complete collecting of data related to the process:
- Leak test values
- Insertion forces and positions
- Torque and anglel values
- Etc.
We study each project in detail in order to adapt to the existing IT systems in our customers' plants, integrating our machines in their information networks.
Conveyor
Customized solutions according to the part to be conveyed, its size and required orientation.
- Palletized conveyors
- Roller chain conveyors
- Belt conveyors
Solutions adapted to customer's process / lay-out requirements:
- Separated input and output conveyors
- Conveyor loops including curves
- Palletized conveyors with lifts at each end and two height lanes
We have the capacity to integrate standard third-party equipment as well as conveyors of our own design. Our product development includes pneumatically actuated stoppers of proprietary design.
TRADEMARKS
Reading
- Within the operations related to traceability, and especially after marking the parts on the machine, it is necessary to check the correct marking or to incorporate the unique part ID to associate the process data to the part.
- Integration of cameras or sensors for 2DM code / QR / Barcode reading.
- Possibility of marking degree evaluation according to the ISO/IEC TR 29158 (AIM DPM-1-2006) standard, by means of special verification units.
TRADEMARKS
Measuring
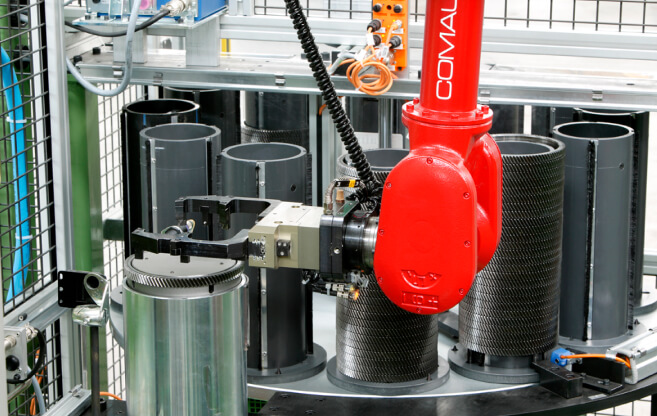
- Possibility of complementing the assemblies by in-process measurements, to guarantee variable dimensions depending on the actual part.
- Measuring systems through integration of third-party equipment or in-house systems using market-standard measuring probes
- We use the measurement units to, for example, generate reference pressing dimensions based on the values obtained, in order to guarantee 100% of the parts.
- When integrating a gauging system, we always include the means for system calibration, either by manual procedures or integrated into the automated system.
TRADEMARKS
Vision
When the conditions of the production line or the floor space available are restricted, there is the possibility of integrating vision equipment to perform various part testing tasks:
- Real-time checking of boring or machining operations on the workpiece.
- Dimensional control of the machined parts.
- Component identification in terms of diversity and positioning.
- Angular or axial components orientation prior to assembly.
- The vision system is carefully studied in each case, analyzing lighting requirements and ambient conditions to ensure a reliable and repeatable process.
TRADEMARKS
Lubrication
- Some assembly processes, especially pressings, require a prior application of lubricant to assist during assembly.
- At Gaindu we have large experience integrating different types of lubrication prior to assembly, using various systems and materials depending on the needs of our customers.
- Lubrication of components or housings, by means of greases or oils of various viscosities. Possibility of additional control by vision of the correct dosing or the quantity of lubrication provided.
Palletizing
- In order to take the automation of a production cell to the next level, automatic palletizing or depalletizing is a high value-added option that completes any production environment through an automatic input and output of parts.
- Using robots and multi-axis gantries, supported when necessary by advanced vision systems, we design and implement automated solutions for the loading of raw parts. From incoming pallets to the unloading of finished parts onto trays, pallets or transport racks.
- Combining these solutions with the traceability solutions offered by Gaindu, an exceptional level of automation and process control is achieved.
Marking
- Within the traceability strategy of the parts produced, their marking is a fundamental step. The marked data uniquely identifies each part and allows the association of process data for future use if necessary.
- We design, manufacture and integrate marking units to etch 2DM / Barcode / QR codes, among others.
- There are several marking alternatives using different technologies: laser marking, micro-percussion or impact marking.
- At Gaindu we design laser marking stations in which we prioritize safety by means of enclosures compatible with Class 4 lasers.
- Due to the experience gained over decades, we are able to integrate the main brands of laser manufacturers in the market or other brands required by our customers.
TRADEMARKS
RFID
- As an alternative or complement to part marking, RFID tags are used in traceability systems on which process data can be written/read.
- RFID tags are mounted directly on the part to be produced (when possible) or on transport pallets attached to them.
- With the combination of tags on parts and readers/writers present on the line's machines, the information is stored so that it can be associated with the part and transferred to an information system or included in a subsequent marking of the part.
TRADEMARKS
Visual Inspection
- As an intermediate control process or as a final part validation process, visual inspection stations are a tool that can be used to check and validate parts.
- At Gaindu we design visual control stations adapted to the needs of the process and the part, with ergonomic functionalities and integrated within our turnkey solutions.
Interested in knowing more how we can help you?
CONTACT US