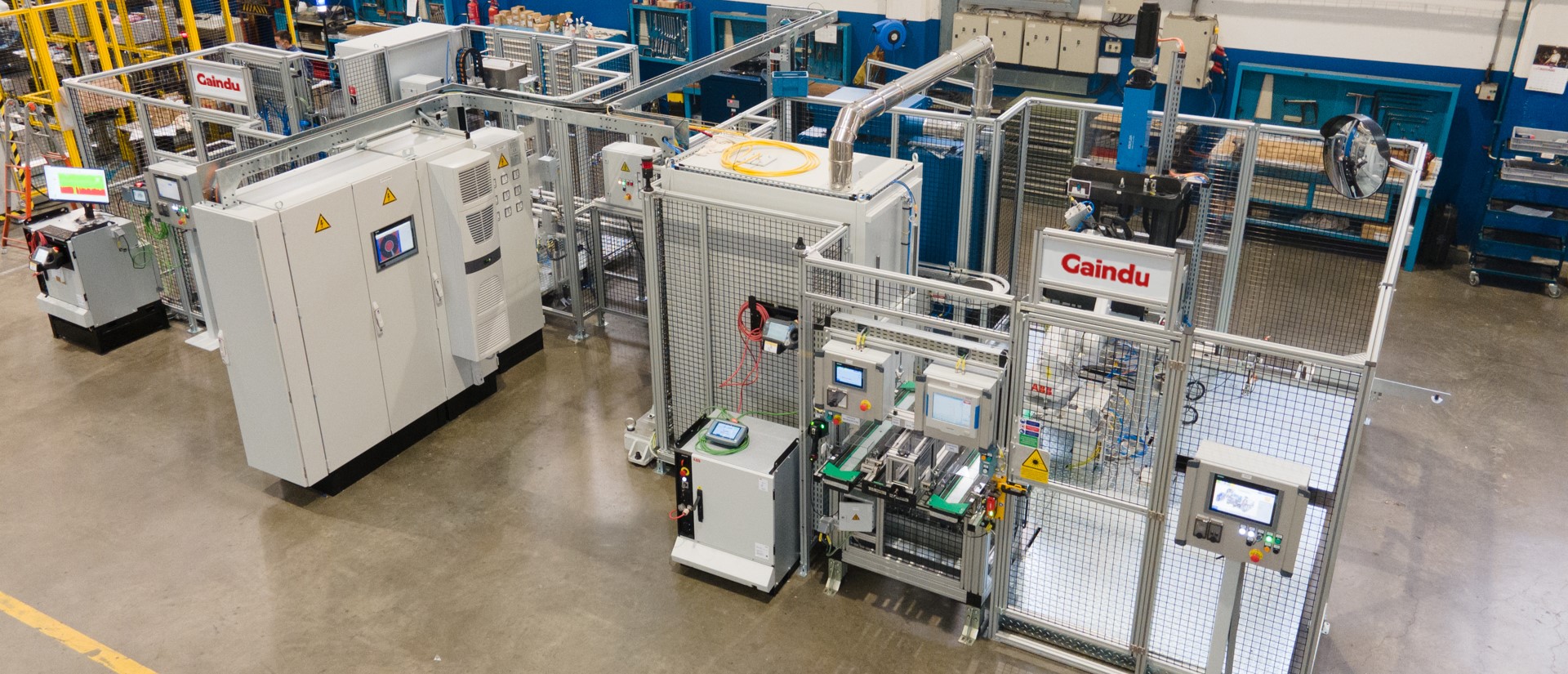
Challenger
Even before the start of the project, when we received the specifications from our customer, we understood that the installation had to meet very high precision requirements due to the tight tolerances contained in the product.
Facing the challenge based on Gaindu's experience in very high precision pressing applications, we were able to achieve the required quality in the final product by combining a full assembly application with laser welding between the two components once they were joined.
The process was then completed with a verification process of the correct welding, in which we combined advanced machine vision systems with an ultrasonic test.
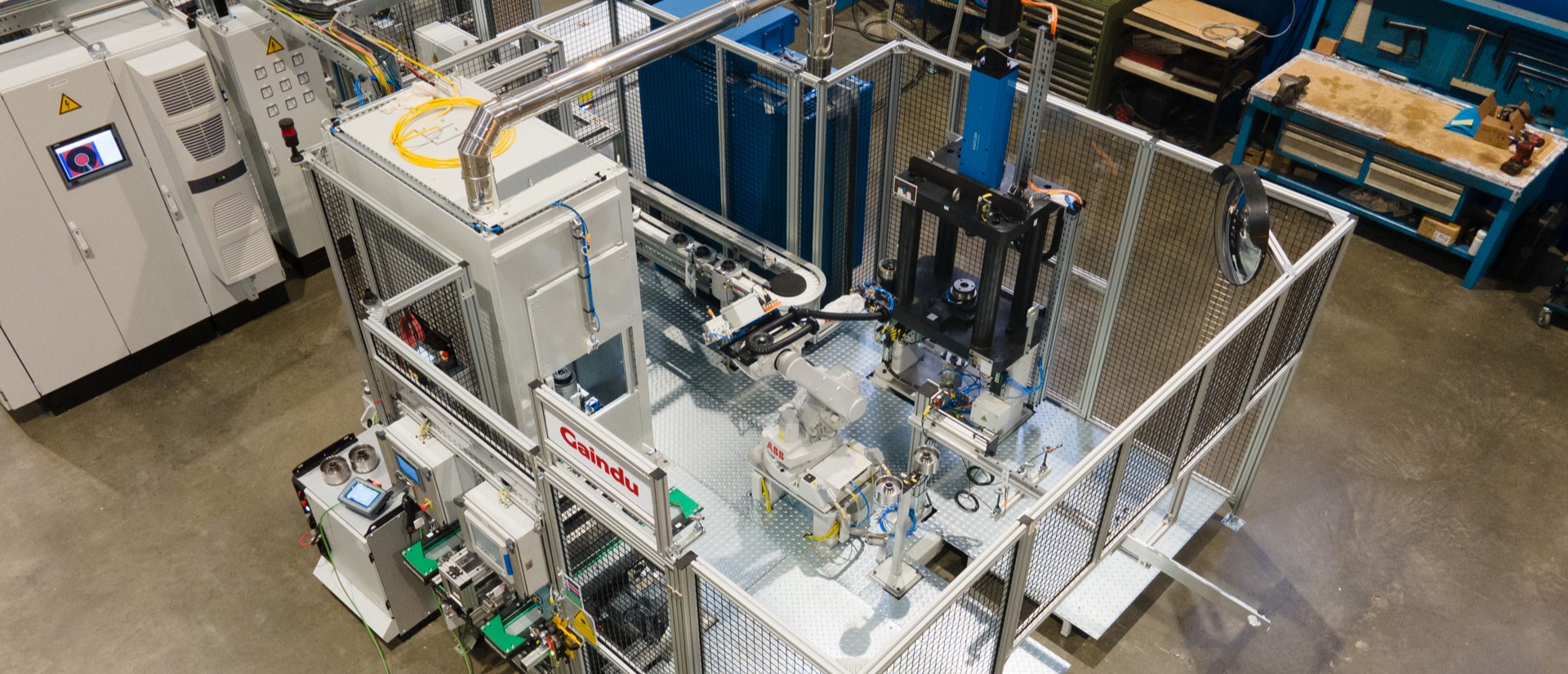
OPERATIONS
Pressing
The initial pressing application consisted of an electric press and a redundant measuring system, which fed the process externally in real time. In this way, the assembly process could be perfectly adapted to the actual condition of the components, individualizing the assembly in each case.
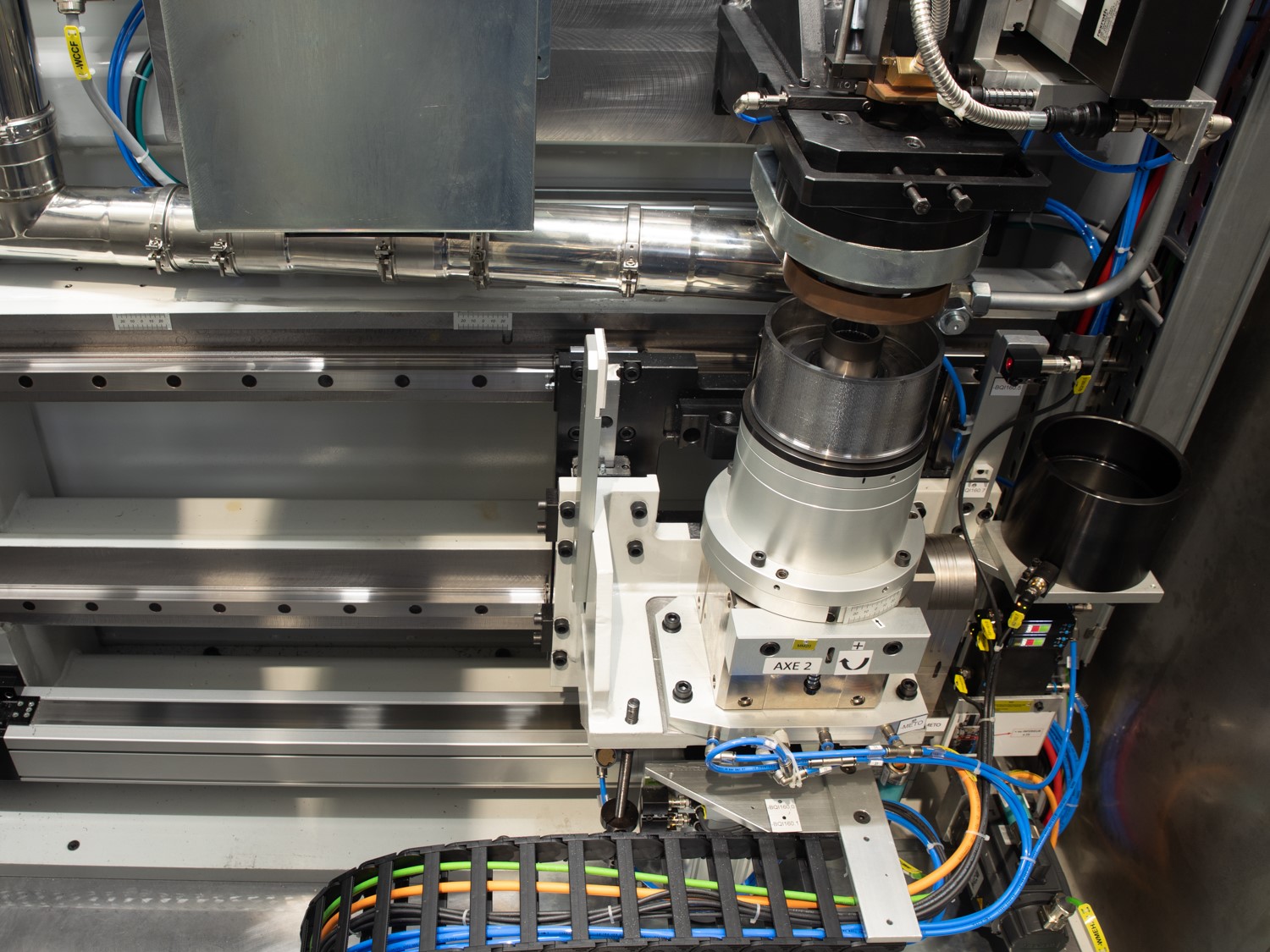
OPERATIONS
Laser welding
After joining the two components by mechanical pressing, the next process consisted of permanently bonding the two parts using a high-power laser welding process.
Our standard concept welding unit, made up of several numerical axes and adaptable to different part diameters, is a crucial tool for a reliable, precise, clean and defect-free rocess. After joining the two components by mechanical pressing, the next process consisted of permanently bonding the two parts using a high-power laser welding process.
Our standard concept welding unit, made up of several numerical axes and adaptable to different part diameters, is a crucial tool for a reliable, precise, clean and defect-free process.
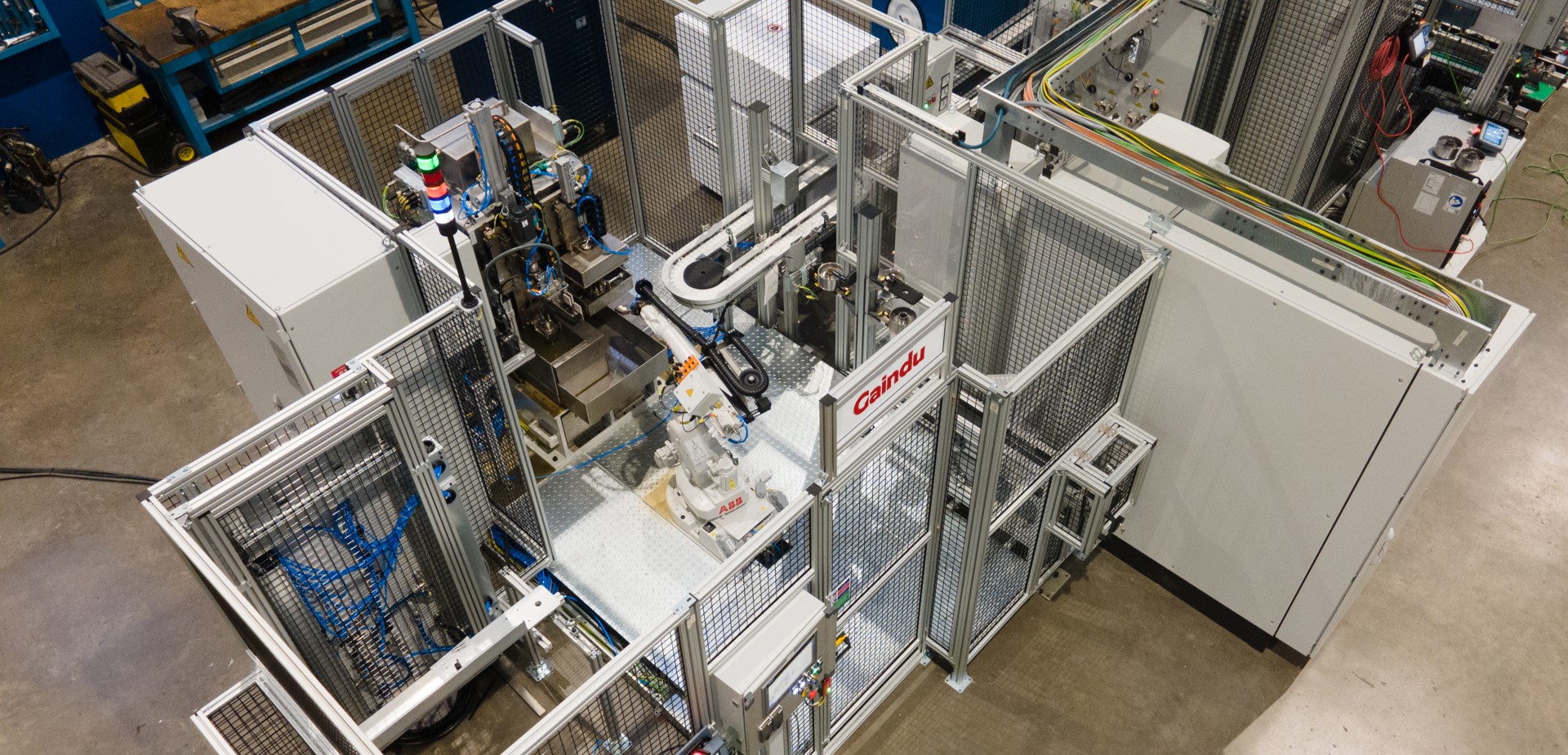
OPERATIONS
Ultrasonic control
Once the parts have been joined, and in this case upon arrival of the assembly to a second robotic cell, a nondestructive post-processing control is performed. This process involves analyzing the complete circumference of the weld seam, using an ultrasonic sensor and specific software. The equipment looks for the different defects that may remain and verifies the correct continuity and depth of the weld in 100% of the parts worked.
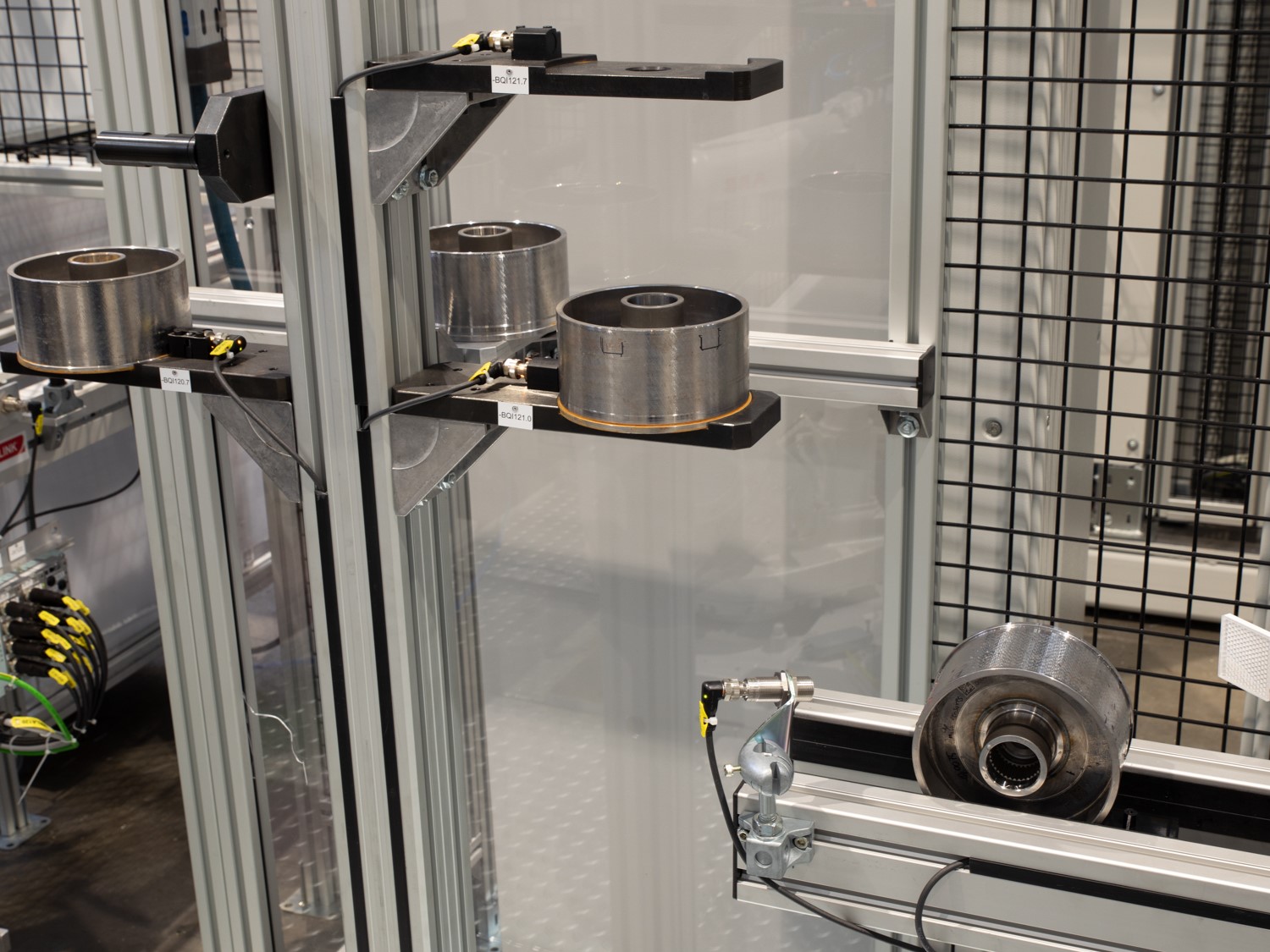
OPERATIONS
Automation
Automation is the system that allows us to link the different stages of the process, making the transition between the different stations automatic, safe and ensuring that the part is not damaged during handling.
The installation contains two complete robotized cells, as well as conveyors for joining, entry and exit of the cells.
Integrated technologies
Interested in knowing more how we can help you?
CONTACT US