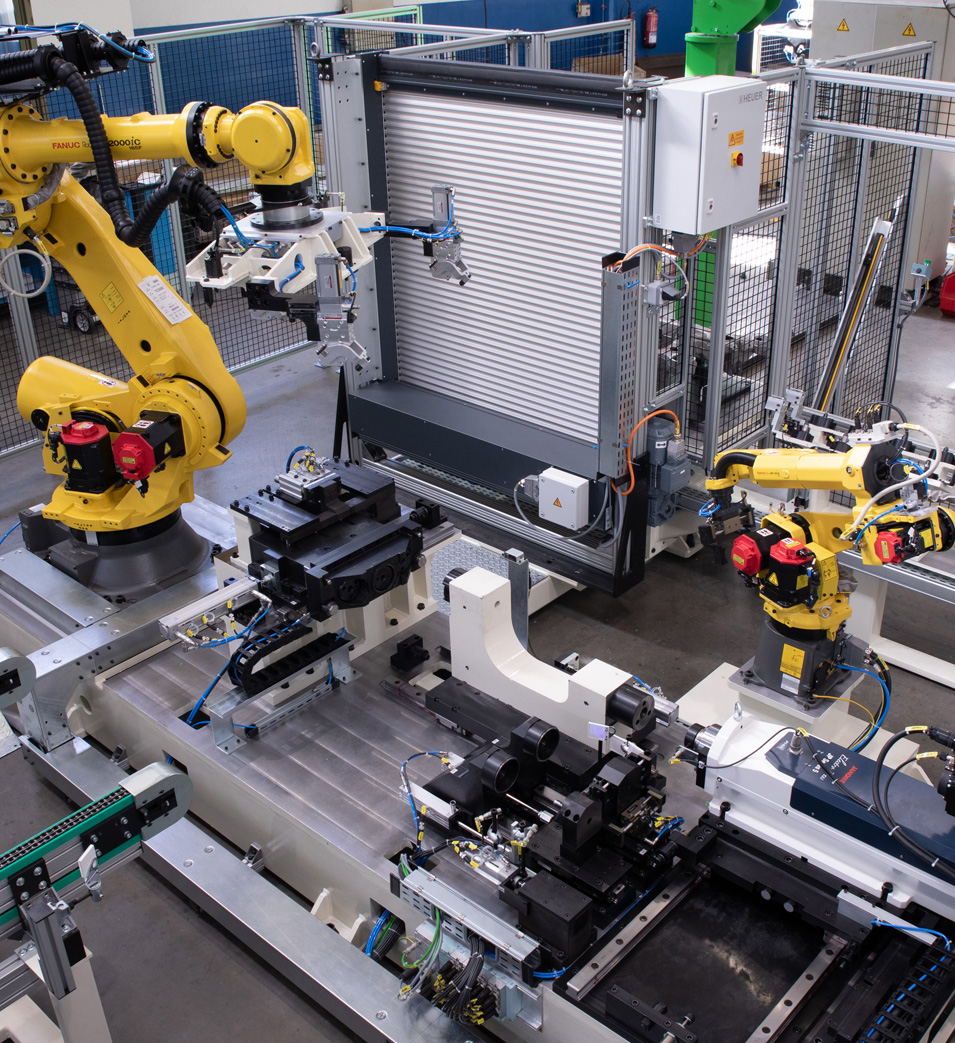
Challenger
The project included the design, manufacture and commissioning of two facilities for the assembly of Front and Rear Subframes for the North American market.
The assembly line concept included two different machines: a first semi-automatic robotized cell for the pressing of bushes in rear subframe and a second manual station for the screwing of two components that form the front subframe.
Due to the specific production requirements for this project, we selected a combined solution of automatic assembly process and manual loading of components, optimizing the work of the cell operator focused on the material supply process.
The designed machine, based on the concepts of flexibility in the assembly through the use of robot for the positioning of parts, includes all the traceability and process data recording in order to guarantee the quality of the finished product, thus complying with the demanding requests of our customer.
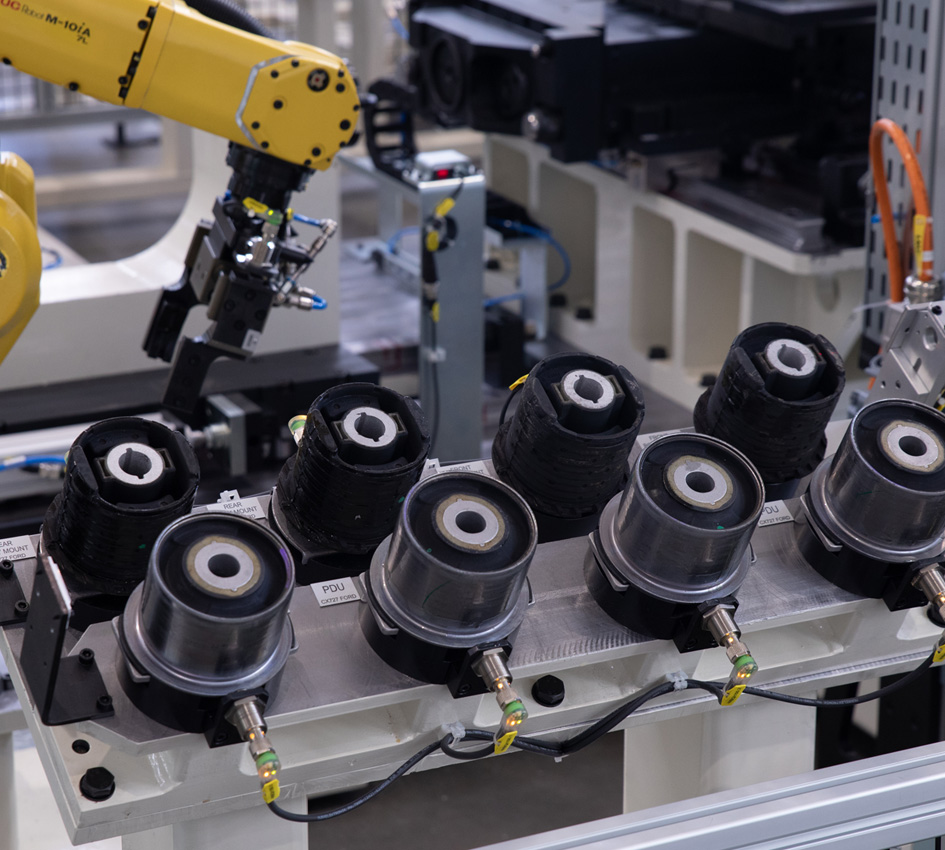
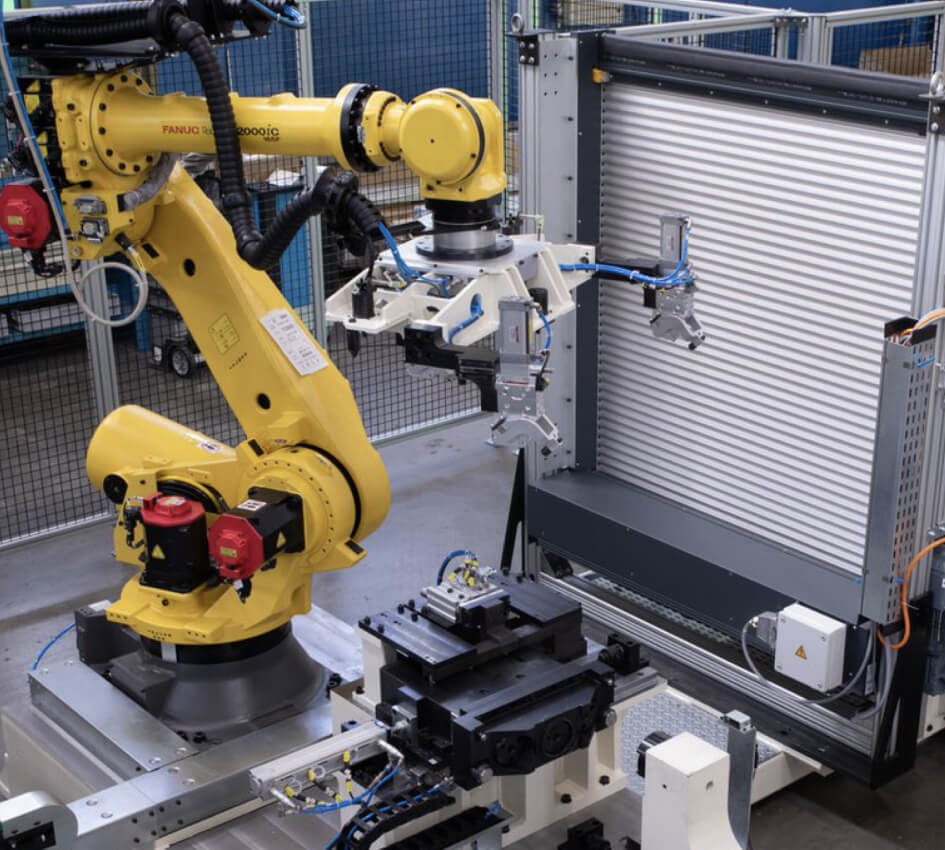
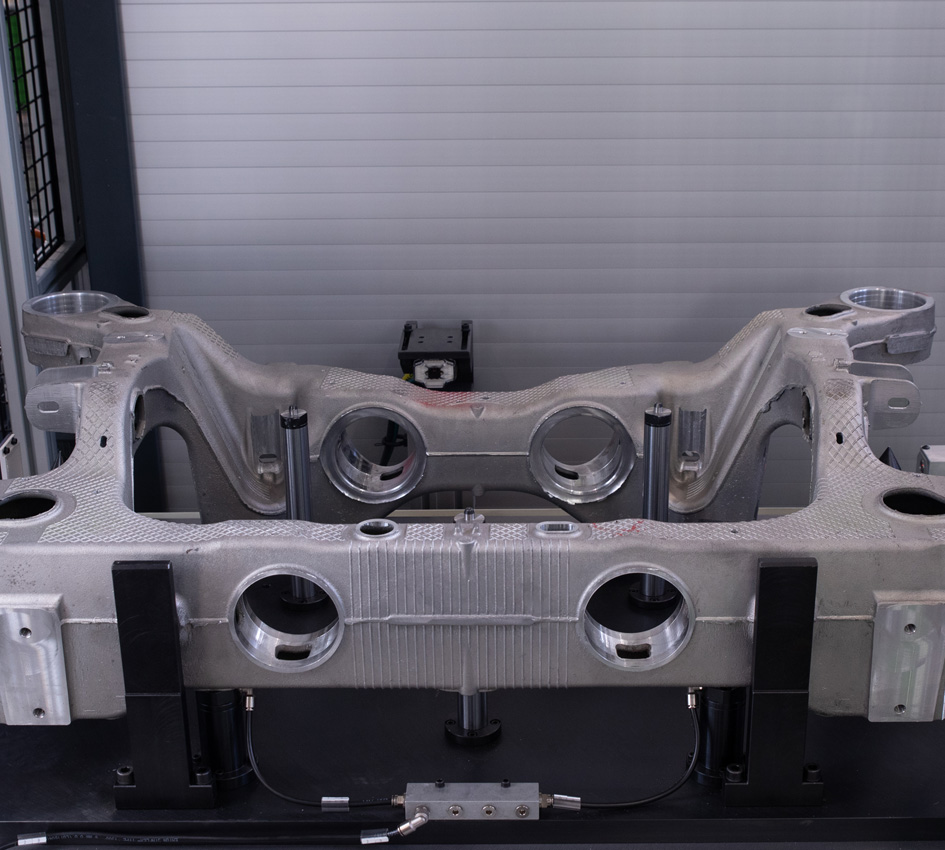
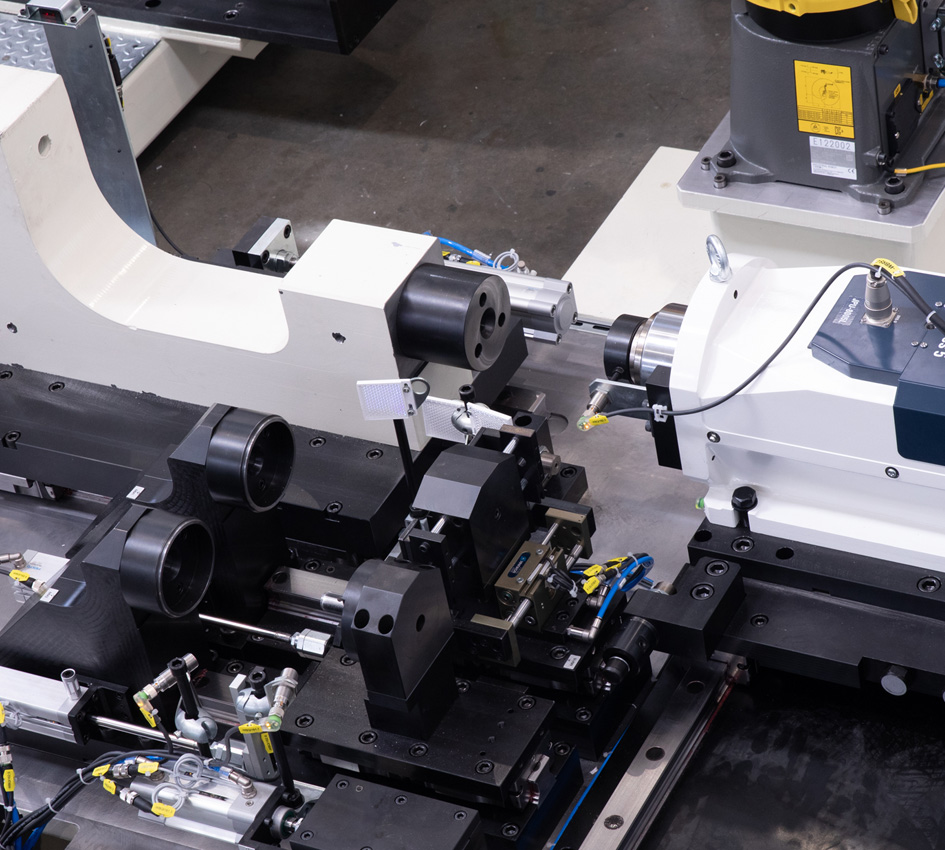
OPERATIONS
Component insertion
The part assembly process is performed as follows:
- A first robot carries out the loading of the components from the manual table to the pressing station.
- The second robot presents the part in its different pressing positions.
All pressing processes are carried out by means of an electric press, controlling the force and insertion height parameters to guarantee the result according to the customer's requirements.
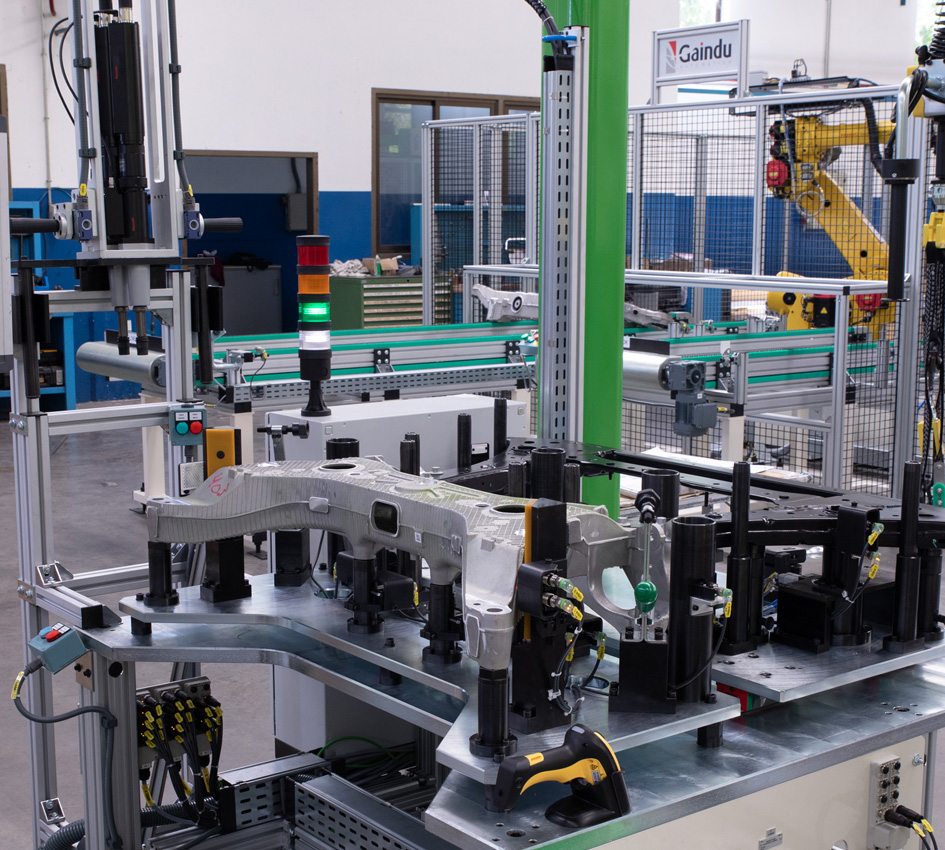
OPERATIONS
Semi-automatic station
The project includes a second machine consisting of a manual station where an operator performs both the work of loading / unloading parts, as well as the screwing with electric screwdrivers.
During the front subframe loading operation, the operator uses a handheld 2DM reader to identify the part and associate the tightening data along with the rest of the parameters registered during the manufacturing process.
Integrated technologies
Interested in knowing more how we can help you?
CONTACT US